In industries like cement plants and mines, material clumping and blockage are common problems. They can lead to production line paralysis and even damage to equipment. Today, we are going to introduce the “Lump Breaker” electric block crusher, which is designed to solve this pain point. As a process engineer with 15 years of experience, I would like to take you on a deeper understanding of its practical value through this article.
What is a Lump Breaker?
Has your company encountered such a dilemma again? The damp cement raw materials clumped in the warehouse, stuck the discharge port, and the entire production line was forced to shut down. The Lump Breaker the agglomerated material to a uniform particle size through high-speed rotating alloy cutting tools. Last year, the B500 model we installed at the Conch Cement Plant successfully reduced downtime caused by material blockage by 83%.
Wide-Ranging Applications
In addition to the cement industry, this equipment also performs well in the chemical and food processing fields. For example, a pharmaceutical company installed a system in its vitamin powder production line. This solved the problem of inaccurate measurements caused by moisture absorption and clumping.
Key Features and Benefits
The Electric Lump Crusher has advanced features that make it highly effective:
Amazing processing capability: The largest model can handle 1000 cubic meters of material per hour, equivalent to the throughput of 5 standard containers
Widely applicable: capable of handling everything from fragile cement clinker to viscous chemical raw materials
High temperature resistance performance: In our on-site testing, we were able to maintain stable operation even after continuous processing of hot materials at 120℃
Energy saving: Low power consumption (B400 model is 1.1 KW, B500+ is 1.5 KW)
Long lifespan: The crusher blades and grille are made of highly durable materials, extending their lifespan by three times
Intelligent anti-jamming (optional): When encountering stubborn clumps, it will automatically reverse, just like the automatic parking function of a car
How the Lump Breaker Works
The Lump Breaker crushes lumps using rotating blades, forcing material through a grid for even discharge. Here’s how it works:
Feeding stage: Agglomerated materials fall into the crushing chamber by gravity
Breaking moment: The high-speed rotating blade instantly shatters the clumps into small pieces
Fine control: The adjustable sieve can control the particle size of the discharged material, just like the grinding adjustment of a coffee machine
Intelligent Protection System
Intelligent protection (optional) – If the block is too hard, the speed sensor will trigger reverse rotation to clear the blockage. If the blockage persists, the system will shut down to prevent damage. This design improves efficiency and reduces downtime.
Lump Breaker in Mining Applications
In mining operations, a good lump breaker isn’t just convenient – it’s profit protection. Ore clumps can:
- Create bottlenecks at the worst possible moments
- Wear out equipment twice as fast
- Mess with your precise measuring systems
Our mining-specific models add:
✓ Extra armor plating for those extra-stubborn ores
✓ Throughput that keeps up with your biggest operations
✓ Safety features for when dust and sparks are concerns
Installing a Lump Breaker can improve overall mining efficiency, make production more stable, and extend equipment maintenance intervals.
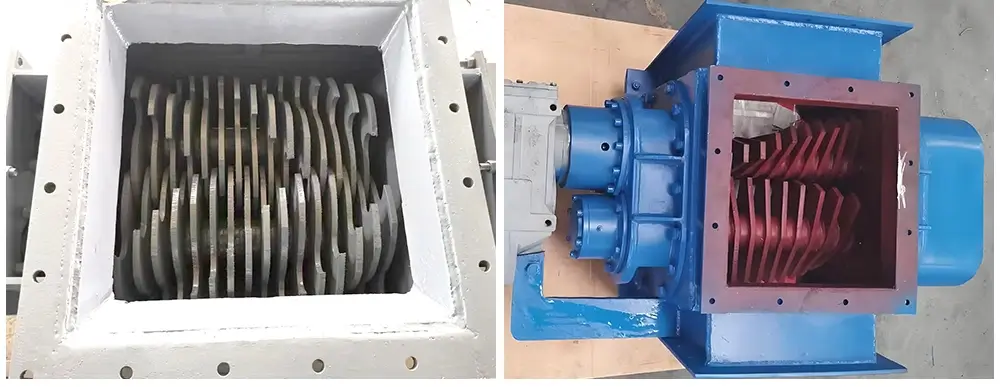
Frequently Asked Questions
Q1: Which industries use Lump Breakers?
A: Besides cement and mining, they are used in chemicals, food processing, pharmaceuticals, and waste management—anywhere lumpy materials cause blockages.
Q2: How to choose the right model?
A: Consider:
Material type (hardness, moisture, size)
Required capacity (B400, B500, etc.)
Working conditions (temperature, safety needs)
Consult a supplier for the best fit.
Q3: How often is maintenance needed?
A: Check every 3-6 months for:
Blade and grid wear
Motor and gear lubrication
Electrical system function
Q4: What if material won’t break?
A: Models with smart sensors reverse automatically. Without this feature, manual clearing is needed.
Q5: How is it installed?
A: It can be horizontal or vertical, usually placed before discharge valves or conveyors.
Conclusion
The Lump Breaker electric block crusher provides an effective solution to material blockage problems across multiple industries, helping to maintain smooth production and reduce downtime.
Need a reliable crusher? Our Lump Breakers offer custom solutions for any application. Contact us today for expert advice!