In the demanding world of industrial operations, maintaining optimal boiler performance is non-negotiable. Efficient fuel combustion is crucial, but it generates significant particulate matter (fly ash). This is where the critical, yet often overlooked, boiler bag filter (or baghouse) comes into play. As an industrial equipment manufacturer specializing in protecting sensitive machinery through voltage stabilization, we understand the intricate dependencies within your plant. Reliable power isn’t just for control systems; it’s vital for environmental compliance systems like your baghouse. This comprehensive guide explores boiler bag filters – their function, importance, maintenance, and why stable power from a high-quality voltage stabilizer is fundamental to their uninterrupted operation.
What is a Boiler Bag Filter?
A boiler bag filter, formally known as a fabric filter or baghouse, is an air pollution control device designed to capture and remove particulate matter (primarily fly ash, unburned carbon, and other combustion byproducts) from the flue gas exhaust stream of an industrial boiler before it’s released into the atmosphere.
Think of it as a massive, high-efficiency vacuum cleaner for your boiler’s exhaust. Instead of disposable bags, it uses hundreds or thousands of long, cylindrical fabric filter bags (or “socks”) housed in a large, compartmentalized structure.
Why Are Boiler Bag Filters Crucial?
- Environmental Compliance: Stringent environmental regulations (like EPA Standards, EU Directives) mandate strict limits on particulate emissions. Bag filters achieve remarkably high collection efficiencies, often exceeding 99.9%, making them essential for legal compliance and avoiding hefty fines.
- Protecting Public Health and Environment: Fly ash contains fine particles (PM2.5, PM10) linked to respiratory illnesses and environmental damage. Bag filters effectively trap these pollutants.
- Operational Efficiency: Clean flue gas paths prevent fouling in downstream equipment like heat exchangers, air preheaters, and stacks, maintaining overall boiler efficiency.
- Resource Recovery: Captured fly ash often has value as an additive in concrete production (pozzolan) or other industrial processes. Bag filters provide a clean, collectible ash stream.
- Plant Safety: Minimizing particulate emissions reduces dust accumulation around the plant site, improving workplace safety and reducing fire hazards.
How Does a Boiler Bag Filter Work?
The core principle is filtration:
- Inlet and Distribution: Hot, ash-laden flue gas from the boiler enters the bag filter through an inlet duct system designed to distribute the gas evenly across the bag compartment.
- Filtration: The gas flows from the outside of the filter bags towards the inside. Larger particles are initially captured on the surface through inertial impaction and interception.
- Cake Formation: Finer particles permeate deeper into the fabric pores but are trapped as a porous layer of collected dust, known as the “dust cake,” forms on the bag’s surface. This dust cake itself becomes the primary filtering medium, enabling the capture of sub-micron particles with exceptional efficiency.
- Clean Gas Outlet: The cleaned gas passes through the fabric of the bag, moves upwards into the clean air plenum, and exits the baghouse via the outlet duct to the stack.
- Cleaning Cycle (Key to Longevity): As the dust cake builds, it increases resistance to gas flow (differential pressure). To maintain efficiency and manageable pressure drop, the bags are periodically cleaned:
- Pulse-Jet Cleaning: The most common method for boiler applications. High-pressure, short-duration blasts of compressed air are fired down through a venturi tube mounted above each bag. This pulse creates a shockwave that travels down the bag, flexing the fabric and dislodging the dust cake into the hopper below. This typically happens row-by-row while the baghouse remains online.
- Reverse Air Cleaning: Gentler method where gas flow is reversed through the bag compartment being cleaned.
- Shaker Cleaning: Mechanical shaking dislodges dust (less common for large, hot boiler applications).
Key Components of a Boiler Bag Filter System
- Housing/Structure: The robust steel enclosure containing the bags and support structure.
- Tube Sheets: Perforated metal plates that physically separate the dirty gas side (lower) from the clean gas side (upper) and provide the sealing surface for the bags.
- Filter Bags: The heart of the system. Made from specialized fabrics (e.g., Fiberglass, P84®, Ryton®, Nomex®, PTFE coatings) chosen for temperature resistance, chemical compatibility with flue gas constituents, and durability. Attached via snap bands, clamp bands, or sewn-in rings to the tube sheet. Supported internally by metal cages to prevent collapse.
- Cages: Wire mesh structures inside each bag preventing bag collapse under vacuum pressure and aiding cleaning efficiency. Typically stainless steel for corrosion resistance.
- Hopper: Conical or pyramidal collection bin at the bottom designed to funnel the dislodged dust cake towards discharge points. Includes access doors, vibrators or rapper pads to prevent bridging, and level indicators.
- Cleaning System (Pulse-Jet): Comprises an air compressor or blower, air storage tank (receiver), manifold, solenoid valves, diaphragm valves, and blow pipes/nozzles precisely aimed down the centerline of each bag row. Requires clean, dry, oil-free compressed air at the correct pressure.
- Differential Pressure Gauges: Monitor resistance across the filter bags, indicating cake buildup and triggering cleaning cycles or signaling problems.
- Inlet/Outlet Dampers: Isolate compartments for maintenance.
- Discharge System: Rotary airlocks, screw conveyors, or pneumatic conveying systems to transport collected ash from hoppers to storage silos or disposal.
- Control System (PLCs/DCS): Automates the cleaning cycle timing (based on time or ΔP), monitors pressures, temperatures, and valve operation, and provides alarms.
Why Your Bag Filter Depends on Stable Power
As a leading voltage stabilizer manufacturer, we understand the critical vulnerability of modern industrial filtration: Unstable Power Supply. Boiler bag filter operation is heavily reliant on consistent, clean power:
1.Control System Integrity: PLCs, instrumentation (pressure transmitters, temperature sensors), and solenoid valves controlling the cleaning sequence demand clean, stable power. Voltage sags or surges can cause control system lockups, erratic valve operation (missed cleaning pulses or continuous pulsing), or sensor errors, leading to:
- Over-cleaning: Premature bag wear, shortened bag life, wasted compressed air.
- Under-cleaning: Excessive pressure drop (ΔP), reduced boiler efficiency due to restricted flow, potential boiler trips on high ΔP.
- Uncontrolled Operation: Complete failure to clean, leading to bag blinding and costly downtime.
2.Compressed Air System: The lifeblood of pulse-jet cleaning. Rotary screw compressors and their sophisticated controllers are highly sensitive to voltage fluctuations. Brownouts or surges can cause compressor trips or erratic operation, depriving the baghouse of cleaning air precisely when needed.
3.Ash Handling Systems: Rotary airlocks and screw conveyors rely on motors. Voltage drops can stall motors, causing ash hoppers to overfill – a major operational hazard requiring immediate shutdown.
A high-quality industrial voltage stabilizer acts as an insurance policy for your boiler bag filter. It ensures:
- Continuous, correct-voltage power to control panels.
- Smooth operation of compressors and ash conveyor motors.
- Protection against surges that fry sensitive electronic components.
- Prevention of unexpected trips and unplanned shutdowns.
- Maximized bag life and minimized maintenance costs.
Protecting your baghouse power supply protects your environmental compliance, boiler efficiency, and bottom line.
Critical Maintenance Considerations for Boiler Bag Filters
Proactive maintenance is essential for longevity and performance:
- Bag Inspection & Replacement: Schedule regular inspections (visual checks, leak detection methods like tribo-electric sensors). Replace torn, abraded, or blinded bags promptly. Remember the dust cake is key – excessive cleaning destroys it.
- Compressed Air System Maintenance: Water, oil, or particulates in the pulse air destroy bags quickly! Ensure dryers and filters are functional. Monitor air pressure and flow.
- Hopper Management: Ash must flow freely. Ensure regular discharge. Inspect for and remove bridging or pluggage. Check insulation/trace heating to prevent condensation and hopper binding.
- Differential Pressure Monitoring: Track ΔP trends. Sudden increases may indicate bag blinding, holes, or cleaning failure. Sudden decreases often signal bag leaks/torn bags.
- Cage Inspection: Bent, corroded, or damaged cages cause bag abrasion and poor cleaning. Replace damaged cages during bag changes.
- Leak Detection: Perform periodic leak testing (e.g., tribo-electric monitoring, optical scanners, or traditional bag leak detectors on stacks) to identify compartment or bag failures early.
- Temperature Management: Monitor inlet gas temperature constantly. Thermal excursions beyond the bag fabric rating are a primary cause of catastrophic failure. Ensure bypass dampers or cooling systems (air dilution or water spray attemperation) function correctly.
- Compartment Isolation Checks: Verify inlet/outlet dampers seal properly to allow safe in-service maintenance.
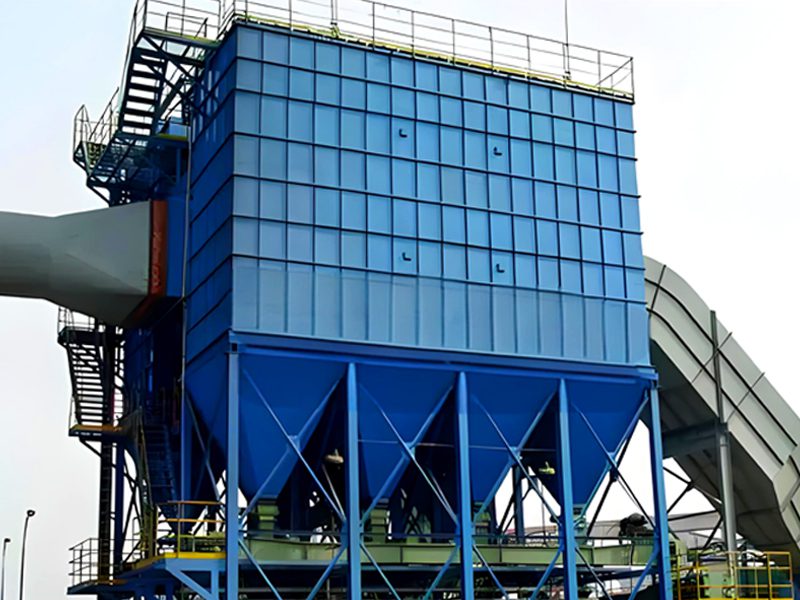
Selecting the Right Boiler Bag Filter Fabric
The choice of filter media is critical and depends on:
- Flue Gas Temperature: Continuous max temp, peak excursions, min temp (avoiding acid dew point).
- Chemical Composition of Flue Gas: Presence of corrosive gases (SOx, NOx, HCl), moisture content, O2 levels.
- Particulate Properties: Abrasiveness, particle size distribution, cohesiveness, combustibility.
- Required Efficiency: Emission limits.
- Cleaning Mechanism: Pulse-jet typically requires felted fabrics; shaker/reverse-air often use woven fabrics.
Common fabrics include PPS (Ryton® – good chemical resistance), Fiberglass (high temp, requires PTFE treatment), PTFE membrane laminates (ultimate efficiency, moisture resistance), P84® (high temp), Nomex® (moderate cost). Consult filtration specialists!
Common Challenges and Solutions
- Problem: Bag Abrasion/Holes: Causes: High gas velocity, abrasive ash, poor gas distribution, damaged cages. Solutions: Optimize duct design/flow modeling, select abrasion-resistant fabrics, inspect/replace damaged cages, install diffusers.
- Problem: Bag Blinding/Difficult Cleaning: Causes: Low compressed air pressure/flow, moisture ingress causing hygroscopic ash, condensation in hoppers/bags, under-temperature excursions. Solutions: Ensure clean, dry compressed air supply, maintain gas temperature above dew point and below fabric max, verify hopper heaters work, check pulse valve function.
- Problem: High Differential Pressure (ΔP): Causes: Excessive dust cake (under-cleaning, dirty pulse air), fine dust loading, bag blinding, fan issues. Solutions: Review and adjust cleaning sequence (pressure, duration, interval), ensure clean/dry air, inspect bags for blinding causes.
- Problem: Ash Bridging/Plugging in Hoppers: Causes: Moisture/condensation, cohesive ash, inadequate hopper slope/volume, failed discharge equipment. Solutions: Ensure functional hopper heaters & insulation, verify ash conditioning additive systems (if used), inspect & repair vibrators/air pads, ensure discharge equipment (rotary valves, screws) function correctly.
- Problem: Thermal Damage: Causes: Exceeding max fabric temp (soot blower activation, process upset), falling below dew point causing acid corrosion. Solutions: Reliable gas temp monitoring/alarms, functional bypass/cooling system, ensure insulation integrity.
The boiler bag filter stands as a guardian at the exit gate of your boiler, protecting the environment, ensuring regulatory compliance, and contributing to efficient plant operations. Its seemingly simple function belies a complex interplay of fabric science, mechanical engineering, and sophisticated controls. Understanding its operation, diligently maintaining its components (especially the vital filter bags and compressed air system), and selecting the right media for your specific flue gas conditions are paramount. Crucially, recognizing the dependency of the baghouse’s electronic controls, instrumentation, and auxiliary equipment on clean, stable power underscores the importance of investing in a robust industrial voltage stabilizer. Protecting the power supply to this critical pollution control device is not just an operational decision; it’s an investment in compliance, reliability, and long-term cost management. By prioritizing both filter performance and power quality, you ensure your boiler operations run cleanly, efficiently, and without costly interruptions.
Frequently Asked Questions (FAQs)
Q: How long do boiler bag filter bags typically last?
- A: Bag life varies tremendously based on flue gas conditions (temperature, chemistry), ash properties, cleaning intensity, fabric choice, and maintenance. Well-maintained bags in suitable conditions often last 2-5 years, sometimes longer. Poor conditions (high moisture, acid dew point issues, thermal excursions) can shorten life to under a year. Strict pulse air quality control is also crucial.
Q: Why is moisture such a problem for boiler bag filters?
- A: Moisture, especially when combined with acidic components in flue gas (SOx, NOx), can cause several issues:
- Dew Point Corrosion: If gas temperature falls below the acid dew point, acids condense on the metal components (cages, tube sheets, housing) and bags, causing rapid corrosion and fabric degradation.
- Ash Plugging: Moisture makes ash hygroscopic (absorbs water), turning it sticky and cohesive. This leads to severe bridging in hoppers, blinding on filter bags (clogging pores, hindering cleaning), and plugging in ash handling systems.
Q: How can a voltage stabilizer specifically prevent boiler bag filter problems?
- A: Voltage stabilizers mitigate risks by:
- Preventing Control System Faults: Stable power avoids PLC/DCS crashes and erratic solenoid valve behavior, ensuring the cleaning sequence runs reliably.
- Protecting Compressors: Ensures consistent voltage to air compressor motors, preventing trips that halt pulse cleaning air supply.
- Avoiding Ash Conveyor Stalls: Keeps discharge system motors running during minor voltage dips, preventing hopper overfills requiring shutdowns.
- Safeguarding Instrumentation: Prevents erratic sensor readings (dP, temperature) that could lead to improper cleaning or bypass damper activation.
Q: What are the signs that my boiler bag filter needs attention?
- A: Key warning signs include:
- Sustained High Differential Pressure: Indicates cleaning inefficiency or bag blinding.
- Visible Stack Emissions: Suggests torn bags or major leaks.
- Spike in Opacity Readings: Continuous Emission Monitoring System (CEMS) data showing increased particulate emissions.
- Frequent Compartment Trips: Due to high ΔP or leaks detected.
- Persistent Ash Plugging: In hoppers or conveyors.
- Increased Fan Power Consumption: Due to high system ΔP resistance.
- Increased Compressed Air Usage Without Cleaning Effect: Points to system issues (low pressure, leaks).
- Physical Inspection Findings: During routine checks (torn bags, damaged cages). Regular monitoring and proactive maintenance are vital to catch issues early.