أساسيات صوامع الأسمنت
1. ما هي صوامع الأسمنت؟
A صومعة الأسمنت هو هيكل تخزين رأسي للأسمنت السائب. له ثلاث وظائف رئيسية:
- يوفر تخزيناً محكم الإغلاق: هذا يمنع الرطوبة والتلوث.
- يعمل مع الأنظمة الهوائية: يسمح بالتغذية الآلية.
- يدمج الوحدات الصناعية: وتشمل الوزن وإزالة الغبار وكسر القوس.
الأنواع الشائعة لصوامع الأسمنت:
- صوامع الصلب الملحومة: الأفضل لسهولة الحمل والتركيب السريع.
- الصوامع الحلزونية: فعالة من حيث التكلفة للمصانع متوسطة الحجم، ومثالية للعمليات ذات الميزانية المحدودة.
- الصوامع الخرسانية: مثالية للتخزين على نطاق واسع، ومناسبة للاحتياجات عالية السعة.
2. كيف تعمل الصومعة؟
تتم عملية تدفق المواد على النحو التالي:
- تملأ مضخات الهواء من الأعلى.
- تتكدس المواد بشكل طبيعي في المخروط.
- يحدث التفريغ من القاع مع تميع الهواء أو الاهتزاز.
- يوفر الناقل اللولبي كميات محسوبة.
المكونات الرئيسية:
- جامع الغبار العلوي (نظام النفث النبضي النفاث).
- أجهزة استشعار المستوى (ترددات الراديو أو نوع الرادار).
- المنشطات المخروطية (القيعان المميعة أو المحركات الهزازة).
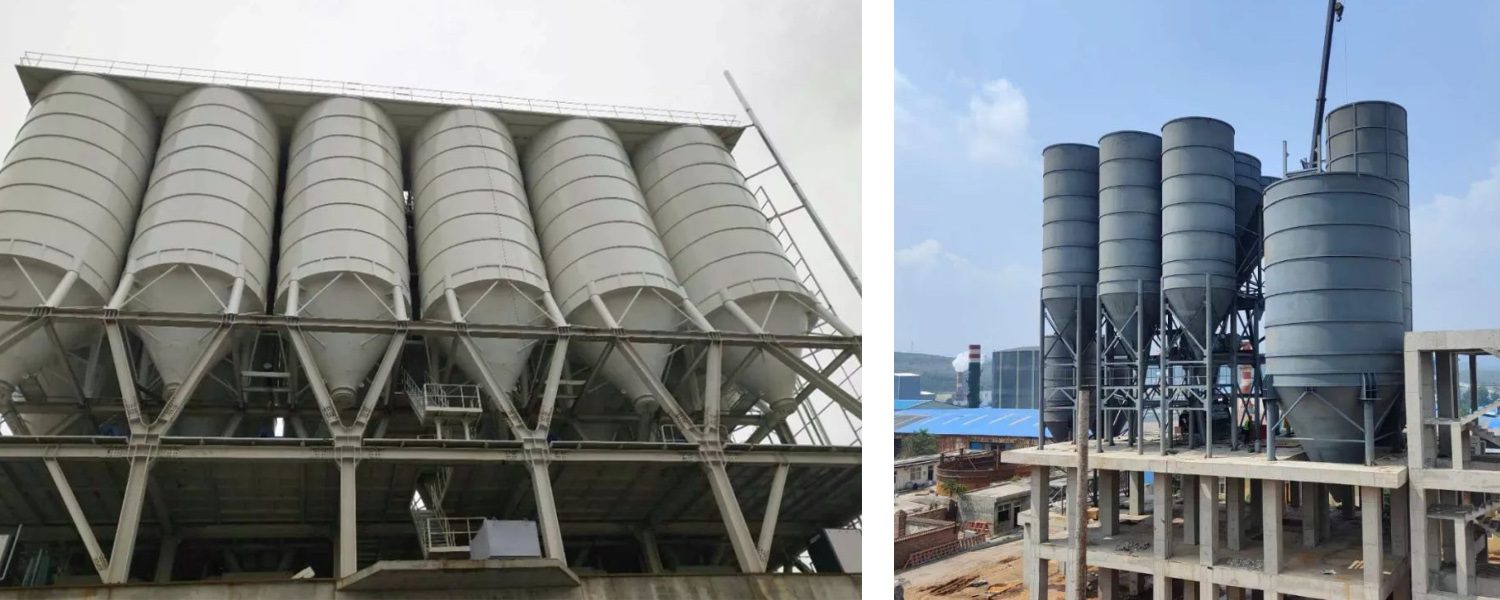
مشاكل صوامع الأسمنت الشائعة
المشكلة الرئيسية ظاهرة التقوس
علامات التحذير:
✔️ لا يوجد تدفق للمواد عند التفريغ (لكن المستوى يظهر طبيعي)
✔️ ارتفاع الضغط غير الطبيعي في النظام الهوائي (+15% من خط الأساس)
✔️ اهتزازات غير معتادة/أصوات ارتطام غير عادية في الصومعة السفلية
بيانات الصناعة:
يزيد التقوس غير المحلول من استخدام الطاقة بنسبة 25-40%
68% من أخطاء الخلط تأتي من ضعف تدفق الصوامع
طرق الوقاية المثبتة
1. التصميم الأمثل للصوامع
الزاوية المخروطية: حافظ على ≥55 درجة (تتجاوز زاوية الاستلقاء الطبيعية للأسمنت)
حجم المخرج: الحد الأدنى 0.2 × قطر الصومعة (على سبيل المثال، تحتاج الصومعة التي يبلغ قطرها 4 أمتار إلى ≥800 مم مخرج)
معالجة السطح: تقلل البطانة الفولاذية المصقولة كهربائيًا من احتكاك الجدار بمقدار 30-40%
2. التحكم في الرطوبة
الأهداف الحرجة:
المعلمة | الهدف | طريقة التحقق |
---|---|---|
رطوبة الأسمنت | <0.5% | اختبار الفقد عند الجفاف |
نقطة ندى الهواء | ≤5 درجة مئوية تحت درجة الحرارة المحيطة | مقياس الرطوبة |
تخزين RH | <60% | مستشعرات تسجيل البيانات |
الإجراءات:
- تركيب أجهزة تنفس مجففة على فتحات التهوية
- سخن الهواء المضغوط إلى 10-15 درجة مئوية فوق درجة الحرارة المحيطة
3. تقنية تعزيز التدفق
المقارنة:
الطريقة | كيف تعمل | الأفضل لـ |
---|---|---|
تمييع الهواء | حقن الهواء منخفض الضغط | المساحيق الناعمة |
الهزازات | التحريك عالي التردد | خلائط حساسة للرطوبة |
المدافع الهوائية | انفجارات الهواء النابضة | تفكك القوس الحالي |
أفضل ممارسات الصيانة
1- الجدول الزمني الوقائي:
- أسبوعيًا: افحص منطقة التفريغ بحثًا عن أي تراكمات
- شهريًا: اختبار أغشية المدافع الهوائية
- ربع سنوي: قياس التآكل المخروطي
2- مناولة المواد:
- استخدم دائمًا FIFO (الوارد أولاً يخرج أولاً)
- تجنب التخزين لأكثر من 30 يومًا
خطوات كسر القوس الطارئة
1️⃣ المرحلة 1 (خلال 30 دقيقة):
إطلاق المدافع الهوائية (≤3 نبضات)
افحص ضغط الهواء المستقر (0.6-0.8 ميجا باسكال)
2️⃣ المرحلة 2 (ساعة واحدة غير محلولة):
التبديل إلى التفريغ الاحتياطي
إضافة معزز التدفق (0.5-1 لتر لكل طن أسمنت)
3️⃣ المرحلة 3 (4 ساعات فأكثر):
التنظيف اليدوي (يتطلب تصريح أماكن محصورة)
افحص تآكل البطانة المخروطية (بدل أقصى ≤3 مم)
الأسئلة والأجوبة التقنية
س: كيف تختار حجم الصومعة؟
ج: استخدم هذه الصيغة:
الاستخدام اليومي (بالأطنان) × أيام التخزين المؤقت (3-7) ÷ الكثافة السائبة (1.1-1.3 طن/متر مكعب) = الحد الأدنى للسعة
س: نصائح حول موسم الأمطار؟
ج: حماية ثلاثية:
الرطوبة: إضافة المجففات المنخل الجزيئي إلى فتحات السقف
البرق مقاومة التأريض <4Ω
ساكنة: مقاومة سطح خرطوم التفريغ <10⁶Ω
الوجبات الرئيسية
- حافظ دائمًا على الزوايا المخروطية > 55 درجة
- راقب الرطوبة كالصقر (<0.5% رطوبة الأسمنت)
- الجمع بين المدافع الهوائية + الهزازات للمواد الصلبة