Dust emissions in steel production account for over 15% of industrial particulate pollution. With stricter environmental regulations, traditional baghouses often fail to meet efficiency standards. Cartridge dust collectors offer a compact, high-performance alternative—but their success depends on correct application. This guide explores how steel plants can leverage cartridge technology while avoiding common pitfalls.
1. Principe de fonctionnement et caractéristiques des dépoussiéreurs à cartouche
1.1 How Cartridge Dust Collectors Work
Dépoussiéreurs à cartouche utilisent des cartouches comme élément filtrant et emploient la technologie du jet d'air pulsé pour le dépoussiérage. Le principe de fonctionnement consiste à aspirer l'air poussiéreux dans le boîtier par la hotte, les conduits et l'entrée d'air. Lorsque le flux d'air se dilate soudainement et interagit avec la plaque de distribution d'air, les particules de poussière les plus grosses tombent directement dans le bac à poussière en raison de la gravité et de l'inertie. Les particules plus petites et plus légères passent à travers la cartouche, où elles sont capturées par le matériau filtrant par diffusion brownienne et effets de tamisage. Après le lavage à contre-courant, la poussière tombe dans le bac à poussière pour être recyclée, tandis que l'air propre est évacué par le tuyau d'échappement à l'aide d'un ventilateur.
1.2 Key Advantages
► OSHA-Compliant Filtration Efficiency:Les cartouches utilisent des fibres de polyester importées comme média filtrant. Elles comportent une couche de fibres submicroniques ultrafines qui bloquent efficacement la plupart des particules de poussière submicroniques, ce qui permet d'atteindre une efficacité de filtration de 99,99% et de respecter les normes d'émission ultra-faibles.
► Low-Resistance Design: Grâce à la grande surface de filtration et à la faible vitesse de filtration, la résistance de fonctionnement ne dépasse généralement pas 1000 Pa. Cela réduit la charge opérationnelle et les coûts du système de dépoussiérage.
►Compact Structure: La conception des cartouches occupe un espace minimal, ce qui facilite l'installation et le remplacement. Les cartouches sont généralement plus courtes que les filtres à poches, ce qui simplifie la construction et l'entretien.
►Long Service Life: The cartridges use imported polyester fibers , achieving 99.99% sub-micron filtration – meeting strict steel plant emission standards.
►Reusable: Les cartouches en polyester et les cartouches recouvertes d'une membrane peuvent généralement être lavées à l'eau et réutilisées, ce qui réduit les coûts d'approvisionnement.
1.3 Limitations to Consider
⚠️ Not for High-Moisture Applications :In humid environments, cartridges can become blocked, requiring downtime for replacements, which affects production efficiency.
⚠️ Higher Cost vs Baghouse Filters: The unit price of the filter cartridge is 5-8 times that of a standard cloth bag, but the overall service life is better.
2. Steel Production Dust Characteristics
Critical Data for Dust Collector Selection:
Production Area | Particle Size Distribution | Moisture Content | Temp Range |
---|---|---|---|
Sintering Material | N/A | >6% | 50-80°C |
Blast Furnace | 76-84% below 200 mesh | <1% | 100-150°C |
BOF Steelmaking | >5μm (98%) | 1.0-1.5% | 80-120°C |
2.1 Zone des matières premières du frittage
En raison des problèmes de transport, les minerais nationaux et étrangers ont généralement un taux d'humidité supérieur à 6%. L'utilisation de hangars de stockage fermés et de systèmes de dépoussiérage par pulvérisation aggrave encore les émissions de poussières.
2.2 Produits frittés et zone de stockage des minerais
1.Les produits frittés génèrent des particules de poussière allant de 0,8 à 61,0 μm pendant le transport, avec un taux d'humidité inférieur à 1%.
2. les hauts fourneaux utilisent généralement des techniques de broyage à chaud, avec des particules inférieures à 200 mesh comprenant 76% à 84%, et un taux d'humidité également inférieur à 1%.
3. pendant le transport du coke, la teneur en humidité est inférieure à 1% pour les processus de trempe sèche, alors que les processus de trempe humide dépassent souvent 10%.
2.3 Zone de transformation de l'acier
1. les flux utilisés dans les convertisseurs ont généralement une teneur en humidité comprise entre 1,01 et 1,5%.
2.Les poussières générées lors du processus de fabrication de l'acier comportent plus de 98% de particules de taille supérieure à 5 μm, avec des températures basses.
3. la teneur en humidité des poussières provenant de la manipulation des scories de convertisseur dépasse souvent 10%.
2.4 Zone de production des aciers pour laminage
Les émissions de gaz humides pendant les processus de laminage dépassent généralement l'humidité 10%, principalement en raison du refroidissement à l'eau.
2.5 Zone de production de la cokéfaction
1.La poussière de charbon générée dans la zone de préparation de la cokéfaction a souvent une teneur en humidité supérieure à 6%, avec plus de 99% de particules de taille supérieure à 2 μm.
2.La taille des particules de poussière pendant le poussage du charbon est généralement comprise entre 3,3 et 4,7 μm, avec une humidité des gaz résiduaires comprise entre 1% et 5%.
2.6 Zone de production du flux
Pendant le transport du calcaire et de la chaux finie, plus de 95% de particules de poussière dépassent 10 μm, avec un taux d'humidité inférieur à 1%.
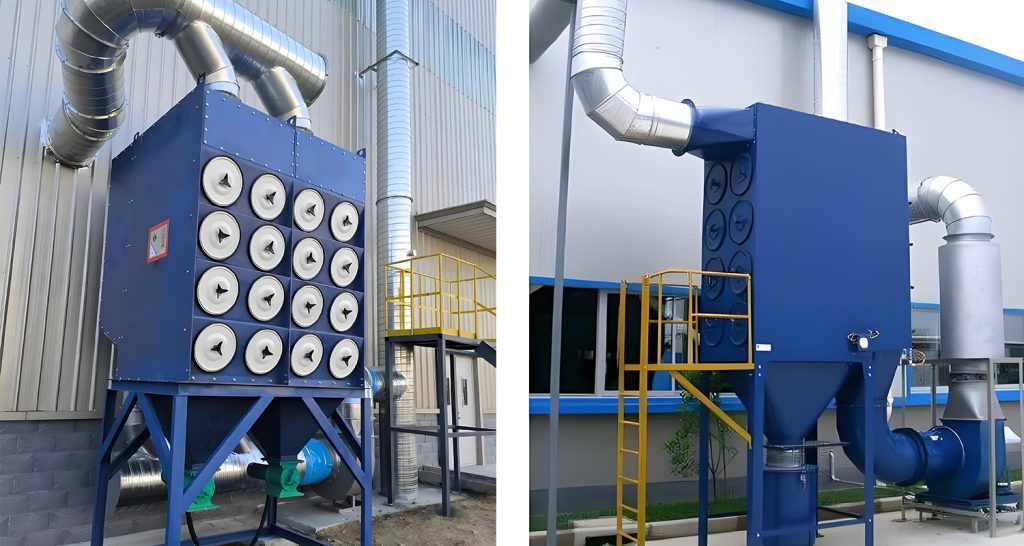
3. Key Recommendations for Cartridge Dust Collector Applications in Steel Plants
① Moisture Control Strategies
Avoid collecting high-humidity waste gas: This includes waste gas from iron ore in the sintering preparation stage and from wet coking processes.
For OSHA-compliant dust control, monitor humidity levels at material transfer points.
② Handling Sticky Particulates
Use caution with sticky waste gas: This applies to dust generated during lime transport and in the coking process.
Note: Sticky dust with >5% moisture content may require pre-treatment.
③ Airflow Optimization
Optimize inlet design: Lower the inlet airspeed of the cartridge dust collector and improve internal airflow distribution to ensure uniform flow among cartridges.
Recommended inlet velocity: ≤1.2 m/s for most steel applications.
④ Pulse Jet System Maintenance
Ensure uniform backflushing airflow: The length of the backflushing nozzle should be maximized to maintain even airflow distribution.
Best practice: Inspect nozzle alignment quarterly.
⑤ Quality Assurance Protocols
Strictly control cartridge quality: Ensure that the technical parameters of folded cartridges meet relevant standards. Inspect the quality of the membrane and uniformity of folds, and verify the manufacturing process of the cartridge seals.
Certification: Look for ISO 16890 compliant filters.
En conclusion, les dépoussiéreurs à cartouches sont très prometteurs pour les entreprises sidérurgiques. Cependant, il est essentiel d'optimiser la conception et les stratégies d'utilisation en fonction des conditions d'exploitation spécifiques afin d'améliorer l'efficacité du dépoussiérage et la rentabilité. Choisissez les dépoussiéreurs à cartouche de Darko pour des performances exceptionnelles et des solutions fiables.
Pour plus d'informations sur nos produits ou pour obtenir des conseils professionnels, n'hésitez pas à contacter nous contacter!