工業用除塵システムの中核部品として、 フィルターバッグ は、セメント、冶金、電力などの産業で広く使用されています。しかし、フィルターバッグの火災事故が頻発しており、経済的損失が大きいだけでなく、従業員の安全や生産継続にも脅威となっています。 本稿では、火災の原因を体系的に分析し、的を絞った予防・管理戦略を提示します。
フィルターバッグとは何ですか?
フィルターバッグは、繊維素材を多層化した気固分離装置で、浮遊粒子を遮断してガス浄化を実現します。 その性能は除塵効率やシステムの安全性に直接影響し、特に耐熱性や帯電防止性などの重要な指標が重要になります。
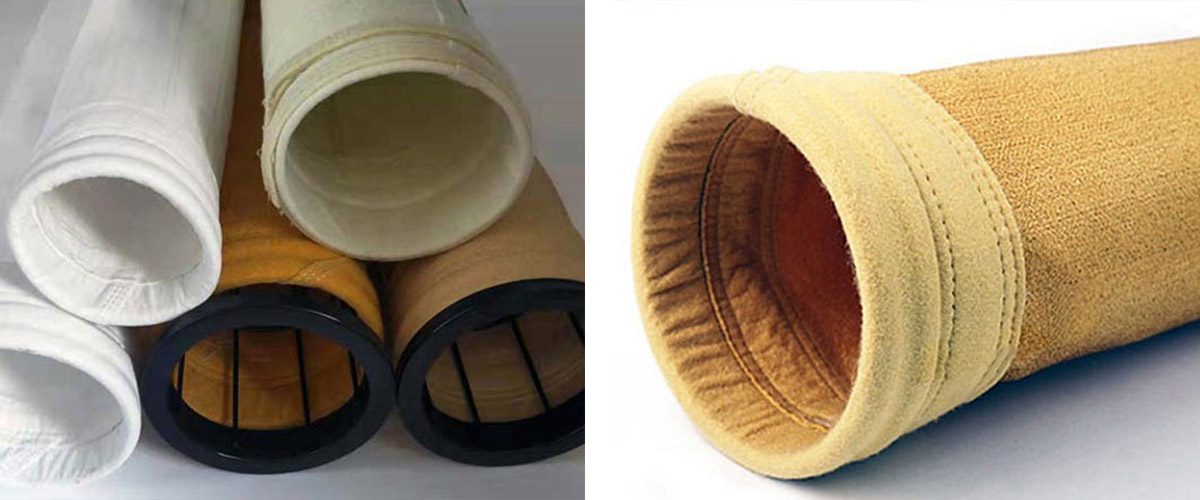
火災原因の深い分析
高温トリガー
1.煙の過熱操作
- 代表的な使用条件冶金用キルン (>300 ℃), セメントロータリーキルン (250-350 ℃)
- 材料の限界:
ポリエステルフィルター素材:130~150℃の高温に耐え続けます。
ノーメックス・フィルター素材:最高204℃の高温に耐えられます。
ガラス繊維フィルター素材:260 ℃まで(シリコンオイル処理)
- 破壊メカニズム:高温による繊維分子鎖の破壊。 80%で強度低下後、火花で引火しやすくなります。
2.局所過熱現象
- 一般的な誘因:
偏った気流分布(測定風速差>30%)
灰洗浄装置の故障(パルスバルブの故障率は15%まで)
熱交換不良(温度差が設計値を50℃超える)
可燃物の蓄積
1.Dust 自然発火の特徴
ダストタイプ | 発火点 (°C) | 最小点火エネルギー (mJ) |
---|---|---|
炭塵 | 160-180 | 30 |
アルミニウムパウダー | 550 | 15 |
硫黄 | 190 | 1.5 |
2.洗浄システムの不具合による影響
酸化熱放出率が300%増加 ダスト層の厚さが 3mm.
ケーススタディ:セメント工場で 5mmの埃蓄積 によるフィルターバッグの 電磁弁の故障 トリガー 自然発火.
静電気放電の危険性
1.発電メカニズム
- ダスト搬送プロセスでは、10~30kVの静電圧が発生します。
- 化学繊維フィルターバッグは、表面抵抗が10 ¹³ Ωを超えると電荷が蓄積しやすくなります。
2.放電着火条件
Energy>0.25mJ はほとんどの産業塵を発火できます
主な防止策カーボンブラックやマグネシウム粉末などの低MIE物質
設備故障リスク
1.機械的な摩耗と損傷
- パルスブロー・エリアでの損傷率は、全体の60%を占めています。
- ベンチュリ・チューブが5°ずれると、気流の侵食が激しくなります。
2.電気的危険
- モータ配線の緩みは 2000 ℃のアークを発生させます。
- 制御盤内のダスト蓄積量が0.5mmに達すると、50%の絶縁性能が低下します。
体系的な予防・管理計画
温度監視システム
1.Three レベルの警報メカニズム:
レベル1警告(10%温度超過):音と光のアラーム
レベル2警告(20%過熱):インターロック冷却
レベル3警告(30%過熱):緊急シャットダウン
廃熱回収技術:
150℃までの冷却範囲を持つGGH熱交換器を設置
ダストクリーニングの最適化戦略
- 圧力時間」デュアルコントロールモードの採用
- 2000パルスごとに膜を手動でチェック
静電気除去対策
- ステンレス鋼導電性繊維のインプラント(含有量≥ 5%)
- イオン風静電気除去装置の設置
設備管理基準
- 日常点検:パルスバルブの作動状況の確認
- 毎月点検接地抵抗<4 Ω
- 年次オーバーホール:老朽化した電気部品の交換
結論
これらの総合的な対策を実施することで、産業界はフィルターバッグ火災のリスクを大幅に低減し、安全で安定した操業を確保することができます。今後も、フィルターバッグの耐火性を向上させ、産業粉塵の取り扱いの安全性を向上させるための新しい技術や方法を探求していく必要があります。
詳細やお問い合わせは下記までお気軽にどうぞ。 お問い合わせ.皆様のお役に立てることを楽しみにしております。