電磁式振動フィーダ は、鉱業、食品加工、セメント、化学プラントなどの産業で効率的なマテリアルハンドリングに不可欠です。摩耗性、高温性、または腐食性の材料を輸送する必要があるかどうかにかかわらず、これらのフィーダは、最小限のエネルギー消費で正確かつ低メンテナンスの動作を保証します。このガイドでは、生産性を最大化し、ダウンタイムを削減するための主な利点、ステップバイステップのメンテナンス、および実証済みのトラブルシューティング方法について説明します。
電磁振動フィーダの動作原理は何ですか?
電磁振動フィーダは、電磁駆動システムによって生成された制御脈動振動によって動作します。通電すると、電磁石が交互に吸引力を発生させ、トラフを前後に高速移動させます(通常1秒間に50~60サイクル)。この運動は、正確な角度のスプリングと組み合わされ、壊れやすい顆粒の穏やかな取り扱いを維持しながら、材料を連続的な流れで前進させるマイクロスローイングアクションを作り出します。供給速度は、半波整流回路を通して入力される電圧を変化させることにより、正確に調整することができます。
電磁振動フィーダーを選ぶ理由5つのメリット
1.スマートオートメーション制御
特徴 半波整流回路 にとって 無段階送り調節自動化された生産ラインに最適です。
2.低メンテナンス設計
回転部分や潤滑が不要 - 運用の複雑さとコストを削減します。
3.摩耗を最小限に抑えた長寿命
マイクロスローイングモーション スクリューフィーダーに比べ、トラフの摩耗が最大40%減少します。
4.耐腐食性と耐高温性
合金鋼トラフ 200°C(392°F)までの材料に対応し、化学腐食に耐性があります。
5.省エネ運転
消費 30%パワーダウン 機械式フィーダーよりも低騒音(<75dB)です。
振動フィーダーにメンテナンスが必要なサイン
これを見てください 注意書き:
異常な振動や衝撃音。
💩 材料の流れが一定しない(供給不足/供給過多)
エネルギー消費量の突然の急増
積極的なメンテナンスにより、80%の故障を防ぎます。
電磁フィーダメンテナンスチェックリスト
1.週次検査
振幅とコイル電流をチェックします(10%を超える偏差は問題を示します)。
異音に耳を傾けてください - 研磨音は、スプリングまたはボルトの故障を示唆しているかもしれません。
2.エアギャップ調整 (重要!)
- 原因トラフの中心線と加振力の線が同一鉛直面上にない。
- 解決策同じ垂直面になるように調整する。
3.スプリングとボルトの締め付け
スプリングの緩みはねじり振動の原因になります。
4.粉塵防止
スプリングにホコリが詰まるのを防ぐため、シーリングカバーは毎月清掃してください。
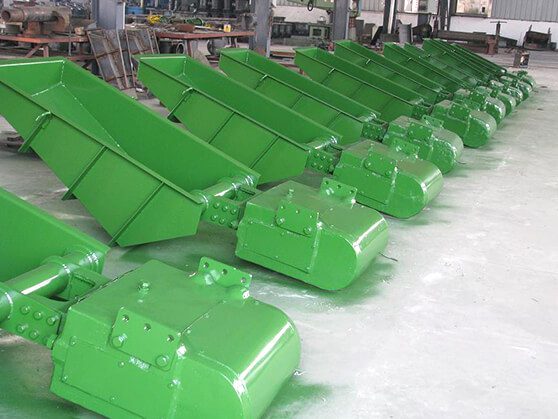
振動フィーダーに関する10の一般的な問題(およびその迅速な解決方法)
問題点 | 原因 | ソリューション |
---|---|---|
電源投入後の振動なし | ヒューズ切れまたはコイルのショート | ヒューズの交換、ワイヤー抵抗のチェック |
材料は横に流れます | トラフとフォースラインのずれ | トラフを垂直に再センタリング |
弱い振動 | サイリスタの損傷またはギャップの詰まり | サイリスタの交換、ゴミの除去 |
大きな不規則なノイズ | スプリング破損・ボルト緩み | スプリングを交換し、ボルトを締めます。 |
大電流動作 | エアギャップが大きすぎる(2.5mm以上) | 隙間を2mmに調整 |
よくある質問
フィーダーはどのくらいの頻度で点検すべきですか?
吾輩輩は猫である、名前はまだない、どこで生れたか頓と見当がつかぬ、何でも薄暗いじめじめした所でニャーニャー泣いていた事だけは記憶しています。
濡れた素材や粘着性のある素材に対応できますか?
A: はい。 ステンレス鋼トラフ および目詰まり防止設計。[カスタムソリューションについてはお問い合わせください。]
平均寿命は?
A: 適切なメンテナンスで7~10年
結論フィーダーの性能を最大限に引き出す
電磁式振動フィーダは、食品から鉱業まで幅広い産業向けに、低エネルギー使用、スマートな自動化、堅牢な耐久性を提供します。このメンテナンスガイドに従い、問題に早期に対処することで、機器の寿命を30%延ばし、コストのかかるダウンタイムを回避することができます。
ご質問やサポートが必要な場合は、お気軽に下記までご連絡ください。 お問い合わせ.プロフェッショナルなサービスとソリューションを提供できることを楽しみにしています!