Introduction: Revolutionizing Industrial Air Filtration
In today’s industrial landscape, effective dust collection isn’t just a regulatory requirement—it’s a critical component of operational efficiency, worker safety, and environmental responsibility. Cartridge dust collectors have emerged as the superior solution for countless manufacturing, processing, and production facilities worldwide. These advanced air filtration systems outperform traditional alternatives by delivering unmatched efficiency in a compact footprint while reducing operational costs.
As industries face increasingly stringent air quality standards and higher production demands, understanding cartridge dust collector technology becomes essential for facility managers, EHS professionals, and operational leaders. This comprehensive guide explores the engineering principles, advantages, and practical applications of cartridge dust collectors—your ultimate resource for making informed decisions about industrial air quality management.
What Are Cartridge Dust Collectors?
Cartridge dust collectors are advanced filtration systems that utilize cylindrical filter elements (cartridges) to capture and remove particulate matter from industrial airstreams. Unlike traditional baghouse collectors that use fabric bags, cartridge systems employ pleated filter media arranged in a tightly packed configuration. This design dramatically increases the available surface area within the same physical space—typically 2-3 times more filtration area than baghouse systems of comparable size.
The fundamental components include: – Pleated filter cartridges (typically 12-15″ diameter, 24-72″ long) – Pulse-jet cleaning system with compressed air – Dust collection hopper – Airlock discharge device – Filter housing with inlet/outlet configurations – Differential pressure gauge
How Cartridge Dust Collectors Work: The Filtration Process
Understanding the operational mechanics of cartridge dust collectors reveals why they’ve become the industry standard:
Dust-Laden Air Entry: Contaminated air enters the collector through strategically positioned inlets, typically designed to create cyclonic motion that separates larger particles before they reach the filters.
Surface Filtration: As air passes through the pleated media, dust particles are trapped on the filter surface. The precise micron rating of the filter media (ranging from 0.3 to 10 microns) determines the size of particles captured.
Cake Filtration: Collected dust forms a porous layer (filter cake) on the cartridge surface, which actually enhances filtration efficiency by trapping smaller particles.
Pulse-Jet Cleaning: When pressure drop reaches a predetermined level (typically 5-6″ w.g.), short bursts of compressed air travel through blow pipes and into each cartridge. This reverse pulse action dislodges the dust cake without interrupting airflow.
Dust Disposal: Dislodged particles fall into the hopper and are discharged through an airlock valve into collection drums or conveyor systems.
Key Advantages Over Traditional Baghouse Collectors
Cartridge dust collectors offer compelling benefits that explain their widespread adoption:
- Higher Filtration Efficiency: Achieve 99.9% efficiency on particles as small as 0.3 microns
- Smaller Footprint: Provide more filtration area in 50-70% less space
- Lower Energy Consumption: Reduced pressure drop cuts fan horsepower requirements by 25-40%
- Reduced Maintenance Costs: Cartridges typically last 18-48 months (vs. 6-18 months for bags)
- Water Resistance: Synthetic media performs reliably in humid environments where fabric bags would blind
- Fire Resistance: Options with flame-retardant media meet NFPA standards for combustible dust
- Continuous Operation: Pulse-cleaning occurs during production without shutdowns
Critical Applications Across Industries
Cartridge dust collectors deliver exceptional performance in diverse industrial environments:
Metalworking & Fabrication
- Welding fume extraction
- Laser/plasma cutting smoke
- Grinding dust collection
- Powder coating operations
Wood Processing
- Sawdust collection from sanding
- MDF processing dust
- CNC router particulate
- Kiln dust management
Pharmaceutical & Chemical
- Handling potent active ingredients
- Chemical powder processing
- Tablet coating operations
- Containment for toxic compounds
Food Processing
- Sugar and flour dust control
- Mixing/blending operations
- Spray-dried powder collection
- Grain handling dust management
Specialty Manufacturing
- Additive manufacturing (3D printing) fumes
- Composite material grinding
- Ceramic powder handling
- Recycling facility dust control
Key Selection Criteria: Choosing the Right System
Selecting an optimal cartridge dust collector involves evaluating seven critical factors:
Particle Characteristics: Consider dust particle size, shape, abrasiveness, and explosivity (refer to NFPA 652 standards for combustible dust).
Airflow Requirements: Calculate CFM needs based on hood design, capture velocity, and process volume (oversizing by 10-15% provides flexibility).
Filter Media Selection:
- Polyester: General-purpose applications, economical
- Nanofiber: Superior efficiency for sub-micron particles
- PTFE Membrane: Chemical resistance, easy cleaning
- Flame-Retardant: NFPA-compliant for combustible dust
Hydrophobic: Moisture resistance for humid environments
Air-to-Cloth Ratio: Typically 3:1 to 4:1 (ft³/min per ft² of filter media) for most industrial applications.
Pulse Cleaning System: Assess compressed air availability and pressure requirements. Advanced models feature variable frequency drives that adjust cleaning intensity based on differential pressure.
Housing Construction: Choose material suited to your environment (galvanized steel, stainless steel 304/316, or specialty coatings).
Regulatory Compliance: Ensure systems meet OSHA, EPA, and local emissions standards. MERV 15-16 ratings are typical for most industrial requirements.
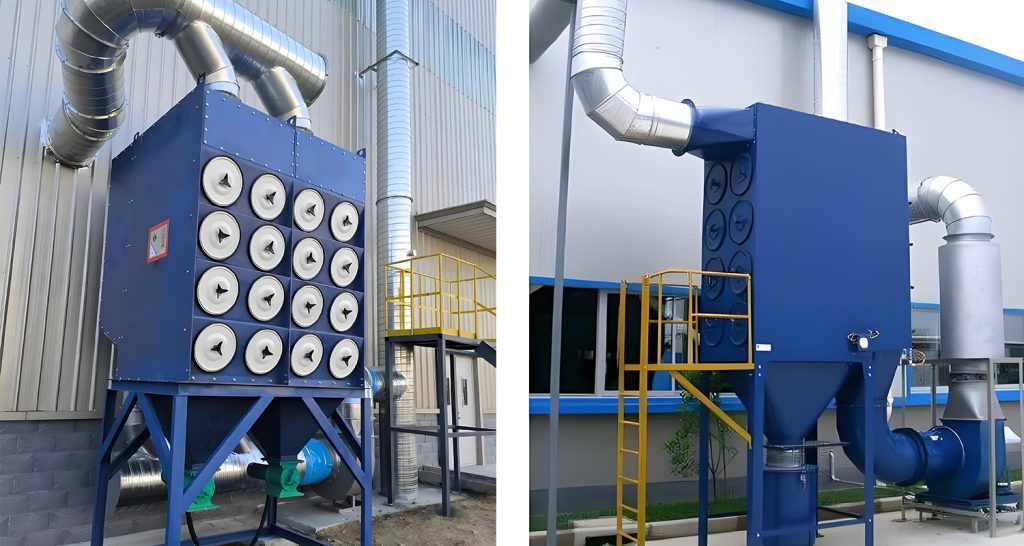
Proactive Maintenance Strategies
Preventative maintenance dramatically extends equipment life and maintains peak performance:
Daily/Weekly Tasks
- Monitor differential pressure gauges (record baseline readings)
- Check hopper discharge for proper operation
- Inspect air compressor for adequate pressure (typically 60-100 PSI)
- Verify dust levels in collection containers
Monthly Procedures
- Perform leak detection with emission monitoring tools
- Inspect filter cartridges for surface damage or plugging
- Check pulse valves and timer operation
- Clean optical sensor lenses
Quarterly/Biannual Maintenance
- Replace damaged filter cartridges following manufacturer guidelines
- Calibrate pressure transducers and sensors
- Inspect housing integrity and gasket seals
- Conduct fan alignment checks
Critical Troubleshooting Areas
- Rising Differential Pressure: Indicates improper cleaning (check air pressure, valve function) or media blinding
- Dust Discharge Issues: Verify airlock function and hopper evacuation
- Visible Emissions: Check for housing leaks or damaged cartridge seals
- Decreased Airflow: Inspect fan operation and system restrictions
Innovations Shaping the Future
Cartridge dust collector technology continues evolving with groundbreaking advancements:
Smart Monitoring Systems: IoT-enabled sensors track performance metrics in real-time, predicting maintenance needs through cloud-based analytics.
Hybrid Collector Designs: Integrated cyclone-cartridge systems achieve multi-stage separation for challenging applications.
Advanced Media Technology: Gradient density filters and specialized membrane treatments enhance efficiency while reducing energy consumption.
Energy Recovery Systems: Heat exchange technology captures thermal energy from exhaust air for facility heating applications.
Robotic Maintenance: Automated cartridge replacement systems eliminate confined space entry requirements.
Sustainable Materials: Bio-based filter media and recyclable components reduce environmental footprint.
Conclusion: Investing in Clean Air, Productivity, and Safety
Cartridge dust collectors represent the pinnacle of industrial air filtration technology, delivering unparalleled efficiency in a compact, energy-saving package. Their superior performance, reduced operating costs, and compliance capabilities make them the smart choice for facilities prioritizing both productivity and safety.
By understanding the operational principles, selection criteria, and maintenance requirements detailed in this guide, you’re equipped to make informed decisions about implementing cartridge dust collection technology. In an industrial landscape increasingly defined by environmental responsibility and operational excellence, these systems provide the foundation for sustainable manufacturing practices that protect workers, equipment, and communities.
Need specific recommendations for your facility? Consult with an experienced dust collection specialist who can perform a comprehensive air quality assessment and provide custom solutions tailored to your operational requirements and compliance needs. Investing in proper dust collection isn’t just about meeting regulations—it’s about building a safer, more efficient, and sustainable industrial future.