Introduction
Cement is an essential construction material, and its quality directly affects the safety and durability of buildings. Therefore, cement production requires strict adherence to standards.During the cement mill’s operation, there’s often a buildup happening. This causes the finished product to be coarser than it should be and also leads to noticeable changes in its chemical makeup. At the beginning of buildup, the content of difficult-to-grind components decreases. As buildup gradually resolves, these components’ proportion increases, directly impacting product quality. Managing and controlling the cement-making process in the cement mill is really important. It helps keep things steady and makes sure the cement is of good quality.
Signs of Buildup
“Buildup,” also known as “full mill” or “blind mill,” occurs frequently during ball mill operations. Signs of buildup include:
- The grinding noise shifts from clear to dull, and the discharge amount decreases.
- The pressure in the inlet and outlet of the drying mill increases.
- The grinding sound might go away, and the main motor’s current drops to around 70% of what it usually is, with a big drop in discharge.
- In severe cases, material may backflow, and no discharge occurs from the outlet.
When inspecting the mill, you may find:
- A thick layer of material on the mill lining, possibly up to 50mm.
- A thick layer of material covering steel balls and segments.
- Severe clogging of the mill’s partition screen.
- About 90% of the effective space in the mill occupied by grinding media and material.
Causes of Buildup
Buildup primarily results from an imbalance between the mill’s feed and discharge, leading to excessive material accumulation in the mill. Specific causes include:
1.When you feed too much material at once, faster than the mill can grind it, it starts to pile up and build up inside.
2.Changes in Material Size: If the particle size of the incoming material increases or its grindability decreases, and the feed rate is not adjusted promptly, buildup occurs.
3.High Moisture Content: Excess moisture in incoming materials and poor ventilation can cause wet material to stick to the grinding media and lining, reducing grinding efficiency.
4.Clogged Partition Screens: Fragments of iron and debris can block the partition screens.
5.Closed Circuit System Issues: A decrease in the efficiency of the classifier leads to excessive recirculation of material.
6.When the amount of grinding media isn’t evenly spread out—like if the first compartment has a lot more than the second—it can cause problems.
7.Damaged Partition Screens: Localized breakage or perforation of partition screens can cause media to move between compartments.
Once buildup occurs, control parameters will show a sharp drop in the mill’s main motor current. The discharge current from the outlet will approach idle levels, indicating severe buildup.
Solutions for Buildup
Upon detecting buildup, you should promptly identify the cause and take action. Common solutions include:
1.Reduce or Stop Feeding: Enhance ventilation within the mill to operate with minimal or no feed, generating more heat.
2.Turning up the heat at the inlet in drying mills helps the moisture evaporate faster.
3.Add Grinding Aids: Add dry coal or limestone to raw material mills, or dry slag to cement mills. Once the grinding noise approaches normal, gradually resume feeding.
4.Gradually Open Exhaust: When addressing buildup in the second compartment, close the exhaust fan damper. Allow material to drop before gradually reopening it to avoid sudden load changes.
In cases of severe buildup, you can use reverse grinding methods to clear the chamber of balls and material. Thoroughly clean the lining and partition screens to restore normal operation.
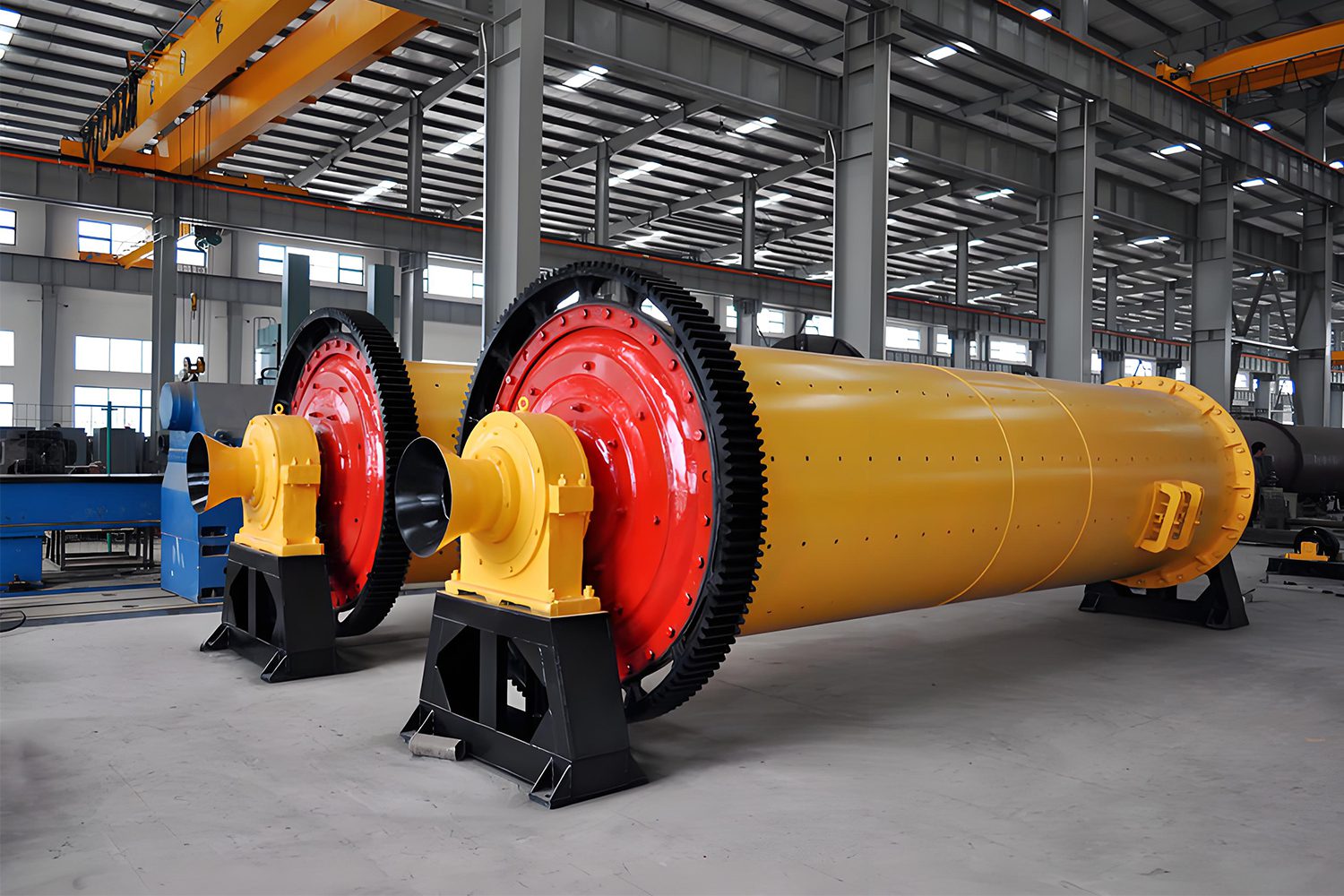
Conclusion
The reasons behind cement mill buildup are pretty varied. Identifying the primary causes and adhering to the principle of “prevention first, elimination second” can help control and eliminate buildup effectively. This approach will lead to high-quality, high-yield, low-consumption, and safe cement production.
For more information about our products and services, please feel free to contact us.