In today’s industrial and commercial landscapes, voltage stability isn’t just a luxury—it’s a critical requirement. Fluctuations in electrical supply can cripple machinery, corrupt data centers, and halt production lines. While voltage stabilizers act as the first line of defense, their core components determine reliability and efficiency. Among these, custom valves (specifically referring to electronic control valves like thyristors or IGBTs in solid-state stabilizers) play a pivotal yet often overlooked role. As a voltage stabilizer manufacturer, we recognize that off-the-shelf valves fail to address unique operational demands. This article dives into why bespoke valve solutions are revolutionizing stabilizer performance, how they’re engineered, and where they deliver unmatched value.
Why Standard Valves Fall Short in Modern Stabilizers
Voltage stabilizers rely on switching mechanisms to regulate input voltage, ensuring consistent output. Generic valves face limitations in complex scenarios:
- Inconsistent Load Handling: Industrial machinery (e.g., CNC units or medical imaging systems) requires millisecond-level response times. Standard valves struggle with erratic loads.
- Environmental Stressors: Extreme temperatures, humidity, or corrosive atmospheres degrade valve integrity.
- Efficiency Losses: Off-the-shelf components often overcompensate for voltage fluctuations, wasting energy.
- Compatibility Gaps: Not all valves integrate seamlessly with IoT-enabled stabilizers or renewable energy setups.
Custom valves resolve these gaps through precision engineering, making them indispensable for critical applications like data centers, manufacturing plants, and healthcare facilities.
The Anatomy of a Custom Valve: Beyond Off-the-Shelf
Custom valves in voltage stabilizers refer to semiconductor-based switching devices (e.g., thyristors, IGBTs, or MOSFETs) tailored to specific electrical and environmental parameters. Unlike mass-produced alternatives, bespoke designs prioritize:
Key Customization Parameters
- Voltage/Current Ratings: Optimized for peak load demands (e.g., 600V/200A for heavy industrial use).
- Thermal Management: Integrated cooling solutions (e.g., copper baseplates) for operations up to 150°C.
- Switching Speed: Ultra-fast response (<5µs) for sensitive equipment.
- Form Factor: Compact designs for space-constrained installations.
- Material Selection: Corrosion-resistant coatings for harsh environments.
Engineering Workflow: From Concept to Deployment
- Requirement Analysis: Collaborate with clients to map load profiles, environmental challenges, and compliance needs.
- Simulation & Prototyping: Use tools like SPICE or ANSYS to model electrical behavior and thermal stress.
- Rigorous Testing: Validate prototypes under extreme conditions (e.g., voltage surges, -40°C to 85°C cycles).
- Production & Integration: Manufacture valves with automated quality control, then test within the stabilizer assembly.
Advantages of Custom Valves in Stabilizer Systems
1. Enhanced Efficiency & Energy Savings
Custom valves minimize switching losses by eliminating over-engineering. For example, a Silicon Carbide (SiC) thyristor reduces energy dissipation by 30% compared to generic silicon counterparts, slashing operational costs.
2. Extended Equipment Lifespan
By precisely matching valve characteristics to load requirements, electrical stress on stabilizers is reduced. Clients report 40% fewer failures in 5-year deployments.
3. Resilience in Extreme Conditions
Case Study: A mining operation in Chile faced voltage dips and acidic air. Custom valves with ceramic encapsulation and enhanced heat sinks cut downtime by 70%.
4. Smart Grid Compatibility
Bespoke valves integrate sensors for real-time current/voltage monitoring, enabling predictive maintenance via stabilizer software.
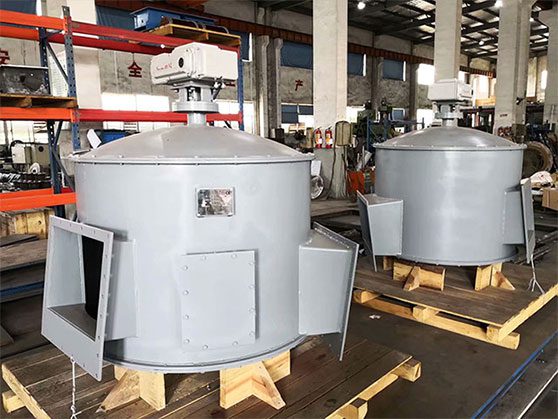
Applications: Where Custom Valves Shine
- Industrial Automation: Synchronous motors in assembly lines demand zero voltage lag.
- Renewable Energy: Solar/wind farms with fluctuating input require adaptive valves.
- Healthcare: MRI machines need ripple-free power to avoid imaging artifacts.
- Data Centers: Prevent downtime with nano-second correction during grid transitions.
Innovations Shaping the Future
- Wide-Bandgap Semiconductors: GaN (Gallium Nitride) and SiC valves enable higher efficiency and power density.
- AI-Driven Optimization: Machine learning predicts load patterns to adjust valve parameters dynamically.
- Modular Designs: Plug-and-play valves simplify upgrades in legacy stabilizers.
Frequently Asked Questions (FAQs)
1. What’s the difference between a standard and custom valve in a stabilizer?
Standard valves are mass-produced with fixed specs, while custom valves are engineered to your unique electrical profile (e.g., voltage range, surge tolerance, and environmental needs). This ensures optimal efficiency, durability, and integration with your equipment.
2. How long does custom valve development take?
Prototyping typically takes 4-6 weeks, depending on complexity. Full deployment (from design to integration) ranges from 8-12 weeks. We expedite timelines using modular architectures for urgent projects.
3. Are custom valves cost-effective for small businesses?
Yes! While upfront costs are 15-20% higher than off-the-shelf parts, custom valves reduce long-term expenses via energy savings (up to 35% lower consumption), fewer replacements, and minimal downtime. ROI often occurs within 18 months.
4. Can custom valves retrofit existing stabilizers?
Absolutely. We design valves compatible with major stabilizer models (including older systems). Retrofitting involves minimal rewiring, preserves your infrastructure investment, and boosts performance by 50%.
Conclusion: Precision Is Non-Negotiable
In voltage stabilization, compromise is a vulnerability. Custom valves transform stabilizers from reactive protectors into proactive power management systems. By aligning valve specs with operational realities, businesses eliminate downtime, slash energy waste, and future-proof critical infrastructure. As a leading manufacturer, we champion this tailored approach—because when it comes to power reliability, “close enough” isn’t an option.
Partner with us to engineer valves that don’t just meet standards—they redefine them.