Cement Silo Basics
1. What is a Silo in Cement?
A cement silo is a vertical storage structure for bulk cement. It has three main functions:
- Provides airtight storage: This prevents moisture and contamination.
- Works with pneumatic systems: It allows for automated feeding.
- Integrates industrial modules: These include weighing, dust removal, and arch-breaking.
Common Types of Cement Silos:
- Welded Steel Silos: Best for portability and quick installation.
- Spiral Silos: Cost-effective for medium-sized plants, ideal for budget-conscious operations.
- Concrete Silos: Ideal for large-scale storage, suitable for high-capacity needs.
2. How Does a Silo Work?
The material flow process is as follows:
- Air pumps fill from the top.
- Materials stack naturally in the cone.
- Bottom discharge occurs with air fluidization or vibration.
- A screw conveyor delivers measured amounts.
Key components:
- Top dust collector (pulse jet system).
- Level sensors (radio frequency or radar type).
- Cone activators (fluidized beds or vibrator motors).
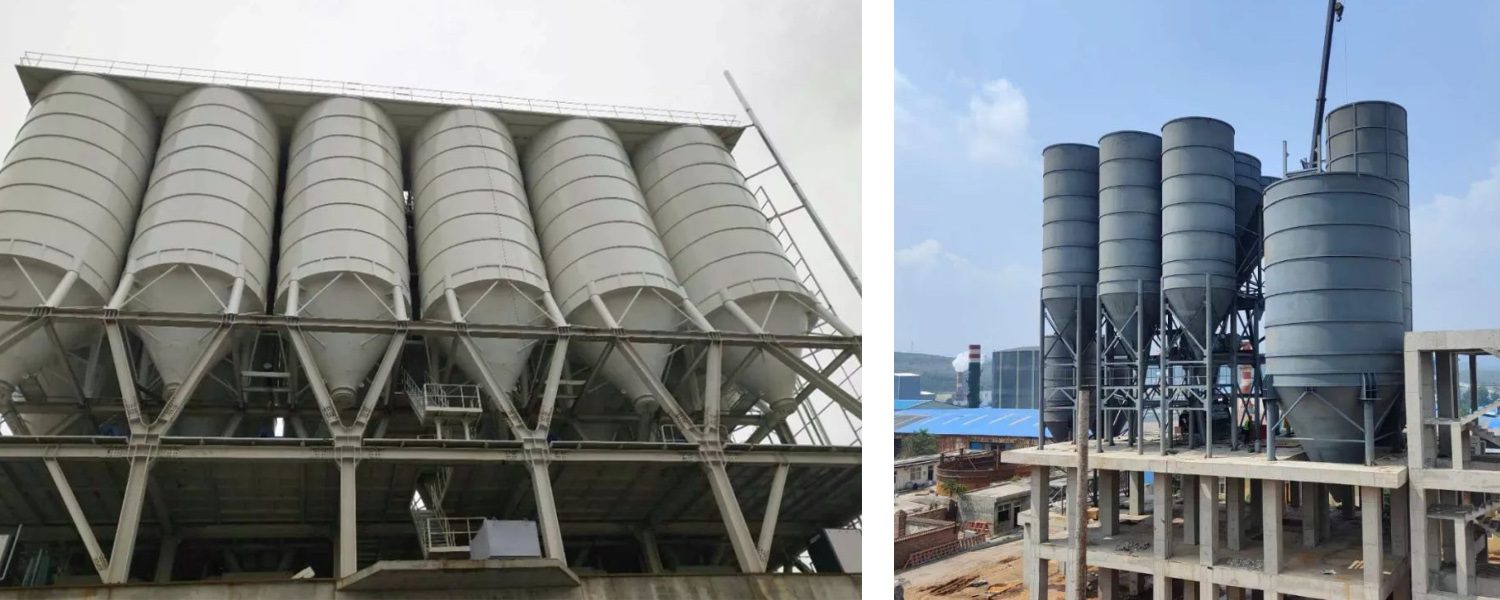
Common Cement Silo Problems
Main Issue: Arching Phenomenon
Warning signs:
✔️ No material flow at discharge (but level shows normal)
✔️ Abnormal pressure rise in pneumatic system (+15% from baseline)
✔️ Unusual vibrations/thumping sounds in lower silo
Industry data:
Unresolved arching increases energy use by 25-40%
68% of batching errors come from poor silo flow
Proven Prevention Methods
1. Optimal Silo Design
Cone angle: Keep ≥55° (exceeds cement’s natural angle of repose)
Outlet size: Minimum 0.2×silo diameter (e.g., 4m silo needs ≥800mm outlet)
Surface treatment: Electropolished steel lining cuts wall friction by 30-40%
2. Moisture Control
Critical targets:
Parameter | Target | Check Method |
---|---|---|
Cement moisture | <0.5% | Loss-on-drying test |
Air dew point | ≤5°C below ambient | Hygrometer |
Storage RH | <60% | Data-logging sensors |
Actions:
• Install desiccant breathers on vents
• Preheat compressed air to 10-15°C above ambient
3. Flow Promotion Tech
Comparison:
Method | How It Works | Best For |
---|---|---|
Air fluidization | Low-pressure air injection | Fine powders |
Vibrators | High-frequency agitation | Moisture-sensitive blends |
Air cannons | Pulsed air blasts | Existing arch breakup |
Maintenance Best Practices
1.Preventive schedule:
- Weekly: Check discharge area for buildup
- Monthly: Test air cannon membranes
- Quarterly: Measure cone wear
2.Material handling:
- Always use FIFO (First-In-First-Out)
- Avoid storage beyond 30 days
Emergency Arch-Breaking Steps
1️⃣ Stage 1 (within 30 mins):
Fire air cannons (≤3 pulses)
Check stable air pressure (0.6-0.8MPa)
2️⃣ Stage 2 (1 hour unresolved):
Switch to backup discharge
Add flow promoter (0.5-1L per ton cement)
3️⃣ Stage 3 (4+ hours):
Manual cleaning (requires confined space permit)
Inspect cone liner wear (max allowance ≤3mm)
Technical Q&A
Q: How to choose silo size?
A: Use this formula:
Daily use (tons) × Buffer days (3-7) ÷ Bulk density (1.1-1.3t/m³) = Min. capacity
Q: Rainy season tips?
A: Triple protection:
Moisture: Add molecular sieve desiccants to roof vents
Lightning: Grounding resistance <4Ω
Static: Discharge hose surface resistance <10⁶Ω
Key Takeaways
• Always maintain cone angles >55°
• Monitor moisture like a hawk (<0.5% cement moisture)
• Combine air cannons + vibrators for tough materials
If you need high-quality cement silos or want to learn more, please contact us. Darko will provide you with professional solutions and excellent service!