Las emisiones de polvo en la producción de acero representan más de 15% de la contaminación industrial por partículas. Con una normativa medioambiental más estricta, los filtros de mangas tradicionales no suelen cumplir las normas de eficiencia. Los colectores de polvo de cartucho ofrecen una alternativa compacta y de alto rendimiento, pero su éxito depende de una correcta aplicación. Esta guía explora cómo las plantas siderúrgicas pueden aprovechar la tecnología de cartuchos evitando los errores más comunes.
1. Principio de funcionamiento y características de los colectores de polvo de cartucho
1.1 Cómo funcionan los colectores de polvo de cartucho
Colectores de polvo de cartucho utilizan cartuchos como elemento filtrante y emplean la tecnología de chorro pulsado para la eliminación del polvo. El principio de funcionamiento consiste en que el aire polvoriento es aspirado hacia el interior de la carcasa a través de la campana antipolvo, los conductos y la entrada de aire. Cuando el flujo de aire se expande bruscamente e interactúa con la placa de distribución de aire, las partículas de polvo más grandes caen directamente al depósito de polvo debido a la gravedad y la inercia. Las partículas más pequeñas y ligeras pasan a través del cartucho, donde son capturadas por el material filtrante a través de la difusión browniana y los efectos de tamizado. Tras el retrolavado, el polvo cae en el depósito de polvo para su reciclado, mientras que el aire limpio se descarga a través del tubo de escape con la ayuda de un ventilador.
1.2 Principales ventajas
► Eficacia de filtración conforme a la OSHA:Los cartuchos utilizan fibras de poliéster importadas como medio filtrante. Presentan una capa de fibras submicrónicas ultrafinas que bloquean eficazmente la mayoría de las partículas de polvo submicrónicas, logrando una eficacia de filtración de hasta 99,99%, cumpliendo las normas de emisiones ultrabajas.
► Diseño de baja resistencia: Gracias a la gran superficie de filtración y a la baja velocidad de filtración, la resistencia de funcionamiento no suele superar los 1000 Pa. Esto reduce la carga operativa y los costes del sistema de captación de polvo.
►Estructura compacta: El diseño de los cartuchos ocupa un espacio mínimo, lo que facilita su instalación y sustitución. Los cartuchos suelen ser más cortos que los filtros de mangas, lo que simplifica la construcción y el mantenimiento.
►Larga vida útil: Los cartuchos utilizan fibras de poliéster importadas , consiguiendo una filtración submicrónica de 99,99% - que cumple las estrictas normas de emisiones de las acerías.
►Reutilizable: Los cartuchos de poliéster y los recubiertos de membrana suelen poder lavarse con agua y reutilizarse, lo que reduce los costes de adquisición.
1.3 Limitaciones a tener en cuenta
⚠️ No apto para aplicaciones de alta humedad :En entornos húmedos, los cartuchos pueden obstruirse, lo que requiere tiempo de inactividad para sustituirlos, lo que afecta a la eficacia de la producción.
⚠️ Mayor coste frente a los filtros de mangas: El precio unitario del cartucho filtrante es de 5 a 8 veces el de una bolsa de tela estándar, pero la vida útil total es mejor.
2. Características del polvo de la producción de acero
Datos críticos para la selección del colector de polvo:
Área de producción | Distribución del tamaño de las partículas | Contenido de humedad | Rango de temperatura |
---|---|---|---|
Material de sinterización | N/A | >6% | 50-80°C |
Alto horno | 76-84% por debajo de 200 mallas | <1% | 100-150°C |
Siderurgia BOF | >5μm (98%) | 1.0-1.5% | 80-120°C |
2.1 Área de la materia prima de sinterización
Debido a los problemas de transporte, tanto los minerales nacionales como los extranjeros suelen tener un contenido de humedad superior a 6%. El uso de cobertizos de almacenamiento cerrados y la supresión del polvo por pulverización agravan aún más las emisiones de polvo.
2.2 Producto sinterizado y área de depósito de mineral
1.Los productos sinterizados generan partículas de polvo de 0,8 a 61,0 μm durante el transporte, con un contenido de humedad inferior a 1%.
2.Los altos hornos suelen utilizar técnicas de molienda con calefacción, con partículas por debajo de 200 mallas que comprenden de 76% a 84%, y un contenido de humedad también inferior a 1%.
3.Durante el transporte del coque, el contenido de humedad es inferior a 1% para los procesos de enfriamiento en seco, mientras que los procesos de enfriamiento en húmedo superan a menudo los 10%.
2.3 Área de la siderurgia de convertidores
1.Los fundentes utilizados en los convertidores suelen tener un contenido de humedad de 1,0% a 1,5%.
2.El polvo generado durante el proceso de fabricación del acero tiene más de 98% de partículas mayores de 5 μm, con bajas temperaturas.
3.El contenido de humedad del polvo procedente de la manipulación de la escoria del convertidor supera a menudo los 10%.
2.4 Área de producción del acero laminado
Las emisiones de gases húmedos durante los procesos de laminación suelen superar los 10% de humedad, debido principalmente a la refrigeración por agua.
2.5 Área de producción de coque
1.El polvo de carbón generado durante la zona de preparación de la coquería suele tener un contenido de humedad superior a 6%, con más de 99% de partículas mayores de 2 μm.
2.El tamaño de las partículas de polvo durante el empuje del carbón oscila generalmente entre 3,3 y 4,7 μm, con una humedad del gas residual entre 1% y 5%.
2.6 Área de producción de fundentes
Durante el transporte de piedra caliza y cal acabada, más de 95% de partículas de polvo superan los 10 μm, con un contenido de humedad inferior a 1%.
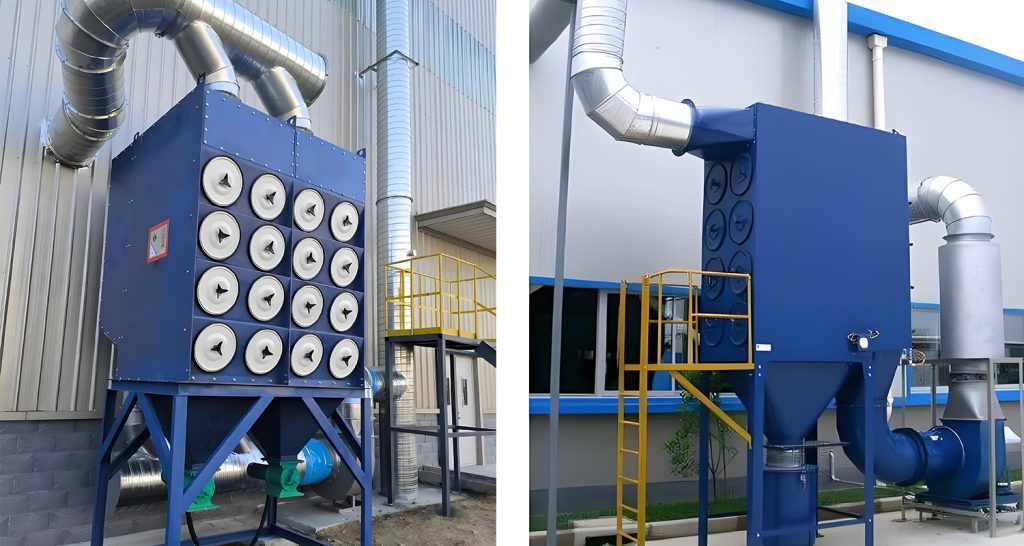
3. Recomendaciones clave para aplicaciones de colectores de polvo de cartucho en acerías
① Estrategias de control de la humedad
Evite recoger gases residuales de alta humedad: Esto incluye los gases residuales del mineral de hierro en la fase de preparación para la sinterización y de los procesos de coquización húmeda.
Para el control del polvo conforme a la OSHA, controlar los niveles de humedad en los puntos de transferencia de material.
② Manipulación de partículas pegajosas
Tenga cuidado con los gases residuales pegajosos: Esto se aplica al polvo generado durante el transporte de la cal y en el proceso de coquización.
Tome nota: El polvo pegajoso con un contenido de humedad >5% puede requerir un tratamiento previo.
③ Optimización del flujo de aire
Optimice el diseño de la entrada: Reduzca la velocidad del aire de entrada del colector de polvo de cartucho y mejore la distribución interna del caudal de aire para garantizar un flujo uniforme entre los cartuchos.
Recomendado Velocidad de entrada: ≤1,2 m/s para la mayoría de las aplicaciones de acero.
④ Mantenimiento del sistema Pulse Jet
Garantice un flujo de aire de retrolavado uniforme: La longitud de la boquilla de retrolavado debe maximizarse para mantener una distribución uniforme del flujo de aire.
La mejor práctica: Inspeccione trimestralmente la alineación de las boquillas.
⑤ Protocolos de garantía de calidad
Controlar estrictamente la calidad de los cartuchos: Asegúrese de que los parámetros técnicos de los cartuchos plegados cumplen las normas pertinentes. Inspeccione la calidad de la membrana y la uniformidad de los pliegues, y verifique el proceso de fabricación de los sellos de los cartuchos.
Certificación: Busque filtros que cumplan la norma ISO 16890.
En conclusión, los colectores de polvo de cartucho son muy prometedores para su uso en empresas siderúrgicas. Sin embargo, es esencial optimizar el diseño y las estrategias de uso en función de las condiciones de funcionamiento específicas para mejorar la eficacia y la rentabilidad de la eliminación del polvo. Elija los colectores de polvo de cartucho de Darko para obtener un rendimiento excepcional y soluciones fiables.
Para más información sobre nuestros productos o para solicitar asesoramiento profesional, no dude en Contacto!