Il s'agit de l'élément central du système de dépoussiérage industriel, sachet-filtre est largement utilisé dans les industries du ciment, de la métallurgie, de l'énergie électrique et autres. Cependant, les incendies de sacs filtrants sont fréquents, ce qui entraîne non seulement des pertes économiques importantes, mais menace également la sécurité du personnel et la continuité de la production. Ce document analysera systématiquement les causes des incendies et proposera des stratégies ciblées de prévention et de contrôle.
Qu'est-ce qu'une poche filtrante ?
Le sac filtrant est un dispositif de séparation gaz-solide composé de matériaux fibreux multicouches, qui permet de purifier le gaz en interceptant les particules en suspension. Ses performances affectent directement l'efficacité du dépoussiérage et la sécurité du système, et les indicateurs clés tels que la résistance à la température et les propriétés antistatiques sont particulièrement importants.
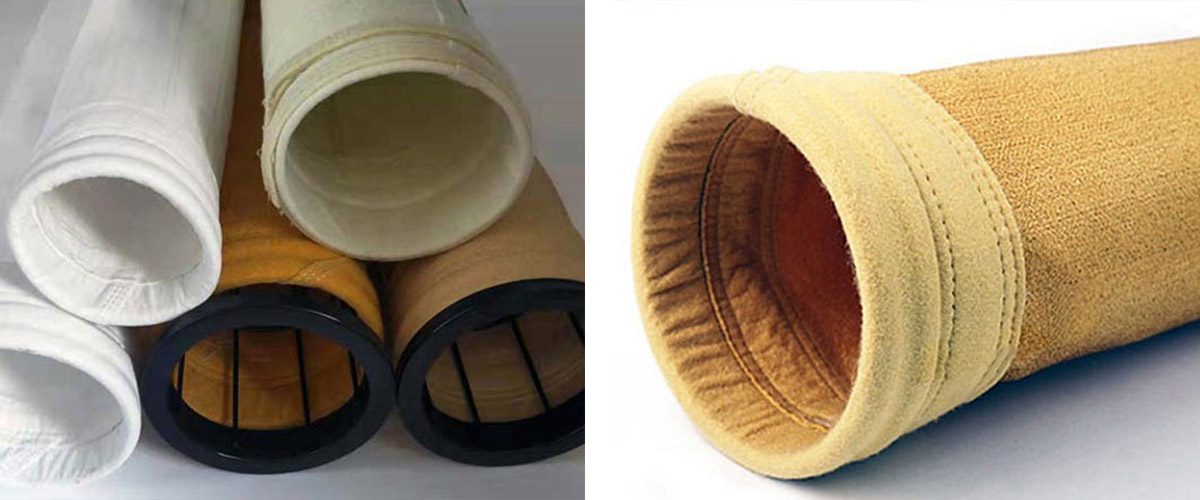
Analyse approfondie des causes de l'incendie
Déclencheurs à haute température
1. Opération de surchauffe des fumées
- Conditions de travail typiques : Four métallurgique (>300 ℃), four rotatif à ciment (250-350 ℃).
- Limite du matériel :
○ matériau filtrant en polyester : peut résister en permanence à une température élevée de 130-150 ℃
○ Matériau du filtre en Nomex : peut résister à une température élevée de 204 ℃ au maximum
○ matériau filtrant en fibre de verre : jusqu'à 260 ℃ (traité avec de l'huile de silicone)
- Mécanisme de rupture : la température élevée entraîne la rupture de la chaîne moléculaire des fibres. Après la diminution de la résistance par 80%, il est facile d'être enflammé par des étincelles.
2. Phénomène de surchauffe locale
- Déclencheurs courants :
○ répartition inégale du flux d'air (différence de vitesse du vent mesurée>30%)
○ défaillance du système de nettoyage des cendres (taux de défaillance de la valve à impulsion jusqu'à 15%)
○ mauvais échange thermique (la différence de température dépasse la valeur de conception de 50 ℃)
Accumulation de matières combustibles
1.Poussière Caractéristiques de la combustion spontanée
Type de poussière | Point d'ignition (°C) | Énergie d'allumage minimale (mJ) |
---|---|---|
Poussière de charbon | 160-180 | 30 |
Poudre d'aluminium | 550 | 15 |
Soufre | 190 | 1.5 |
2. Conséquences d'une défaillance du système de nettoyage
Le taux de dégagement de chaleur par oxydation augmente de 300% lorsque l'épaisseur de la couche de poussière dépasse 3mm.
Étude de cas: Dans une cimenterie, 5mm d'accumulation de poussière sur les manches filtrantes en raison de défaillance de l'électrovanne déclenché combustion spontanée.
Risques de décharges électrostatiques
1. Mécanisme de production d'électricité
- Le processus de transport des poussières peut générer une tension statique de 10 à 30 kV.
- Les sacs filtrants en fibres chimiques sont susceptibles d'accumuler des charges lorsque la résistance de surface est supérieure à 10 ¹³ Ω
2. Conditions d'allumage de la décharge
L'énergie>0,25mJ peut enflammer la plupart des poussières industrielles
Principales mesures de prévention : Substances à faible MIE telles que le noir de carbone et la poudre de magnésium
Risque de défaillance de l'équipement
1. Usure mécanique
- Le taux de dommages dans la zone de soufflage de l'impulsion représente 60% du total des dommages.
- Une déviation du tube de Venturi de 5° entraîne une érosion accrue du flux d'air.
2. Risques électriques
- Un câblage de moteur mal fixé peut générer un arc de 2000 ℃.
- Lorsque l'accumulation de poussière dans l'armoire de commande atteint 0,5 mm, les performances d'isolation diminuent de 50%.
Plan de prévention et de contrôle systématique
Système de contrôle de la température
1. mécanisme d'alerte à trois niveaux :
Alarme de niveau 1 (10% surchauffe) : Alarme sonore et lumineuse
Avertissement de niveau 2 (20% surchauffe) : Refroidissement par interverrouillage
Avertissement de niveau 3 (30% surchauffe) : arrêt d'urgence
Technologie de récupération de la chaleur perdue :
Installez l'échangeur de chaleur GGH, avec une plage de refroidissement allant jusqu'à 150 ℃
Stratégie d'optimisation pour le nettoyage des poussières
- Adoption du double mode de contrôle "temps de pression".
- Contrôler manuellement la membrane toutes les 2000 impulsions.
Mesures d'élimination de la statique
- Implanter des fibres conductrices en acier inoxydable (teneur ≥ 5%)
- Installation d'un éliminateur d'électricité statique pour le vent ionique
Normes de gestion des équipements
- Inspection quotidienne : Vérifiez l'état d'action de la vanne d'impulsion
- Inspection mensuelle : Résistance de mise à la terre<4 Ω
- Révision annuelle : remplacement des composants électriques vieillissants
Conclusion
En mettant en œuvre ces mesures globales, les industries peuvent réduire de manière significative le risque d'incendie des manches filtrantes, garantissant ainsi des opérations sûres et stables. Les recherches futures devraient continuer à explorer de nouvelles technologies et méthodes pour améliorer la résistance au feu des manches filtrantes et la sécurité de la manipulation des poussières industrielles.
Pour plus d'informations ou de demandes de renseignements, n'hésitez pas à contacter nous contacter. Nous nous réjouissons de pouvoir vous aider.