En ciment le processus de refroidissement est essentiel pour garantir la qualité et les performances du produit. Deux méthodes principales sont utilisées : refroidissement en ligne et le refroidissement après stockage. Le refroidissement post-stockage, avec ses large plage de refroidissement et contrôle précis de la températureest idéal pour les applications nécessitant une gestion thermique stricte. Pour maximiser l'efficacité et la longévité de l'équipement, plusieurs facteurs clés doivent être pris en compte lors de la mise en œuvre.
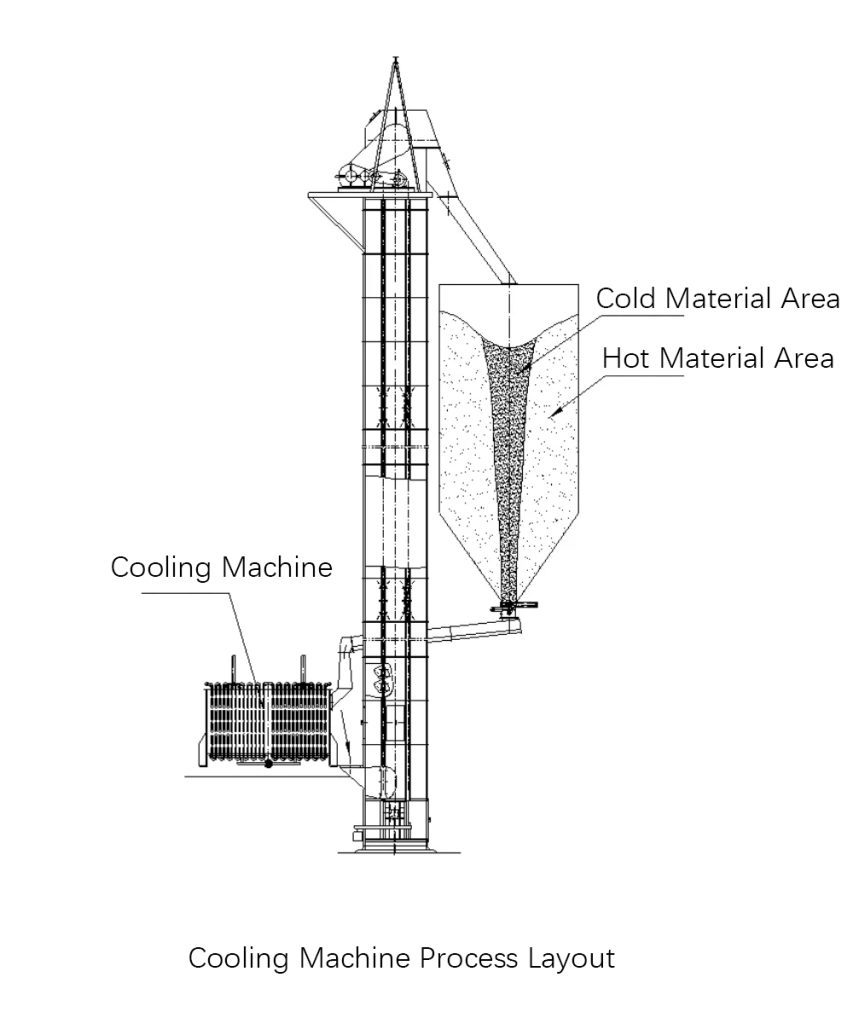
1. Surmonter les inefficacités locales en matière de refroidissement
Dans un processus de refroidissement à silo uniqueLe ciment sort du silo, passe par le refroidisseur et revient par un élévateur. Toutefois, cette méthode peut entraîner un refroidissement inégal : alors que la température de sortie du refroidisseur est conforme aux normes, le matériau de sortie du silo peut rester trop chaud. Ce phénomène est dû à canalisation des flux de matièresoù seule une partie du ciment circule, laissant le reste insuffisamment refroidi.
Solution :
Adoptez un processus de refroidissement à double silo. Le ciment du silo A passe à travers le refroidisseur dans le silo B. Si les températures restent élevées, le matériau peut retourner dans le silo A pour un nouveau refroidissement. Cette méthode garantit distribution uniforme de la température et le respect des normes de qualité.
2. Prévention de la prise en masse du ciment dans les silos
Les fluctuations de température pendant le stockage entraînent souvent une altération du ciment gâteau sur les parois des silosen particulier dans les silos en acier. Lorsque le niveau de ciment baisse, des morceaux peuvent se détacher et pénétrer dans le refroidisseur, ce qui risque d'entraîner une baisse du niveau de ciment. des blocages mécaniques ou des dommages à l'équipement.
Solution :
Installer dispositifs de décolmatage du pré-refroidisseur pour briser les touffes avant qu'elles n'atteignent le refroidisseur.
Ajouter ports d'inspection pour l'entretien régulier et l'élimination des matières encrassées.
3. Éviter les problèmes liés au boîtier d'expansion
Lorsque le ciment déborde du logement du refroidisseur, l'action mécanique peut provoquer expansion des matériauxCe qui entraîne des déformations du logement, des blocages ou des défaillances de pièces. Cela se produit généralement lorsque les débits des silos dépassent la capacité des refroidisseurs ou des élévateurs.
Solution :
Utiliser stabilisateurs de débit sous le silo pour réguler les débits et éviter la surcharge du système.
Conclusion : Optimiser le refroidissement du ciment en termes de qualité et d'efficacité
La conception et l'entretien corrects du processus de refroidissement sont essentiels pour production de ciment de haute qualité. En s'adressant à les déséquilibres locaux de refroidissement, le mottage et les risques d'expansionLes fabricants peuvent ainsi améliorer l'efficacité et prolonger la durée de vie des équipements.
Besoin de conseils d'experts sur les solutions de refroidissement du ciment ?
Contactez nous dès aujourd'hui pour bénéficier d'une assistance sur mesure et d'une expertise de premier plan !