Cement ball mills are the backbone of modern cement plants, playing a critical role in reducing clinker into the fine powder essential for cement production. As energy-intensive industrial equipment, their reliable operation hinges on stable electrical supply. This guide explores how cement ball mills function, their core components, operational challenges, and why voltage stability is non-negotiable for efficiency and longevity—particularly where voltage stabilizers become mission-critical.
How Does a Cement Ball Mill Work?
Cement ball mills operate on the principle of impact and attrition: 1. Loading & Rotation: Clinker (cement’s primary ingredient), gypsum, and additives are fed into a rotating cylinder partially filled with grinding media—typically steel balls.
2. Grinding Action: As the mill rotates (typically at 15–25 RPM), balls cascade and collide, crushing clinker particles through impact and abrasion.
3. Particle Separation: Ground material moves toward the mill’s discharge end. An air classifier separates fine particles (finished cement) from coarse ones, which recycle for regrinding.
4. Output: Final cement powder exits via discharge grates, ready for storage or packaging.
Key Components of a Cement Ball Mill
- Rotating Cylinder: Horizontal steel shell lined with wear-resistant plates (e.g., manganese steel).
- Grinding Media: Steel balls (50mm–90mm diameter); size and composition are material-specific.
- Drive System: High-power motor (~3,500–10,000 kW), reducer gearbox, and pinion.
- Bearings: Trunnion or slide-shoe bearings support the cylinder.
- Liners: Replaceable internal plates protect the shell and optimize grinding efficiency.
- Classifiers: Separators like grit cones or dynamic air classifiers control particle size.
- Cooling System: Water sprays or air jets prevent overheating.
Why Voltage Stability Matters in Ball Mill Operations
As the SEO editor for a voltage stabilizer manufacturer, we emphasize that mills require consistent, high-quality power. Here’s why:
- Motor Protection: Voltage fluctuations cause current surges, overheating windings, and premature motor failure.
- Process Stability: Unstable voltage disrupts mill speed, leading to inconsistent particle size and wasted energy.
- Gearbox Stress: Irregular torque from power instability accelerates wear in reducers and bearings.
- Downtime Costs: A 500-ton/hour mill losing 8 hours to voltage issues can cost >$50,000 in lost output.
- Energy Efficiency: Stable voltage ensures optimal motor performance, reducing kWh/ton energy consumption.
Voltage stabilizers act as insurance—smoothing spikes, sags, and harmonics to shield your mill and ROI.
Common Challenges & Solutions
1. Overheating
- Cause: Excess friction, poor ventilation, or voltage-induced current imbalance.
- Fix: Install voltage stabilizers for balanced phase loads; enhance cooling systems; monitor liner wear.
2. Inconsistent Grind Quality
- Cause: Media wear, classifier blockage, or power supply inconsistency altering mill speed.
- Fix: Calibrate classifiers; implement stabilizer-backed voltage regulation; routine media audits.
3. High Energy Consumption
- Cause: Low motor efficiency (due to voltage drops), poor material feed control, or worn components.
- Fix: Use stabilizers to maintain voltage ≥95% of rated value; optimize ball size; install VFDs.
4. Bearing/Gear Failures
- Cause: Electrical imbalance stressing mechanical parts; inadequate lubrication.
- Fix: Deploy stabilizers to eliminate voltage transients; enforce predictive maintenance schedules.
5 Essential Maintenance Tips
- Voltage Monitoring: Track input voltage 24/7 with stabilizer-integrated alerts.
- Liner & Ball Inspection: Measure wear monthly; replace if thickness drops 50%.
- Lubrication: Use automated systems for trunnion bearings and gears.
- Alignment Checks: Laser-align motor, gearbox, and pinion quarterly.
- Vibration Analysis: Detect unbalance or bearing defects early via sensors.
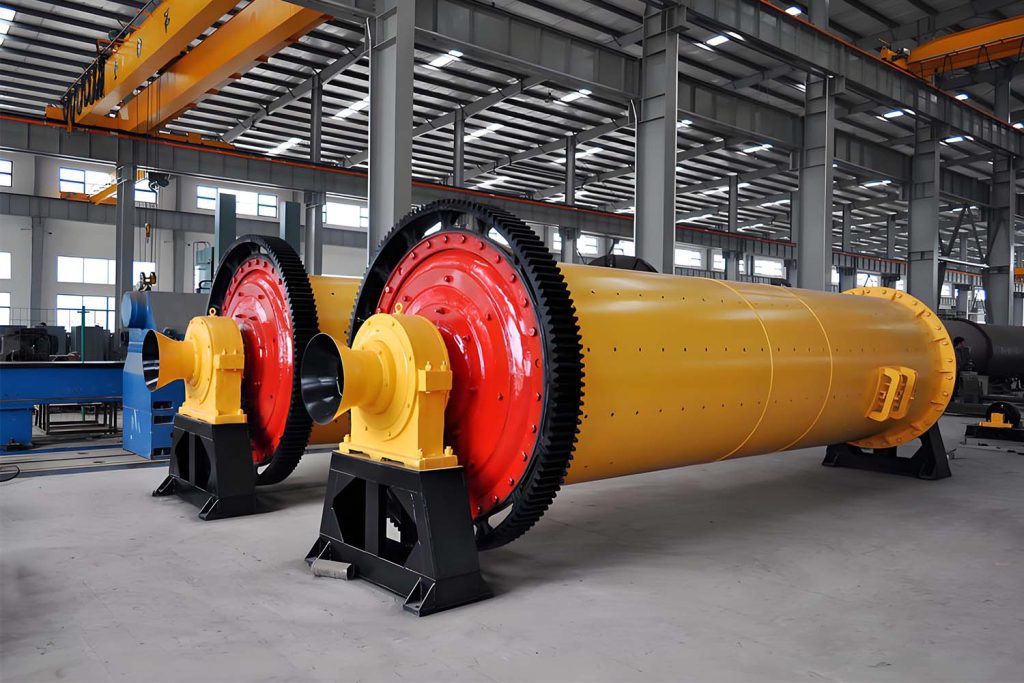
Conclusion: Stability Drives Profitability
Cement ball mills are engineering marvels—and power hogs. Protecting them from voltage instability isn’t optional; it’s foundational to throughput, energy savings, and component life. As a voltage stabilizer specialist, we’ve seen mills extend operating lifespans by 20%+ with robust power conditioning. Partnering with an expert stabilizer provider ensures your grinding process runs like clockwork, maximizing uptime and minimizing costly surprises.
Key Takeaway: Don’t let power volatility grind your profits to a halt. Secure your mill with industrial-grade voltage stabilization.
FAQs About Cement Ball Mills
What’s the typical energy consumption of a cement ball mill?
Cement ball mills use 15–25 kWh per ton of cement produced. Energy efficiency hinges on: – Optimized grinding media load
– Precise voltage/power factor control
– Modern classifier systems
Up to 30% savings are achievable with voltage stabilizers and process audits.
Can voltage stabilizers reduce ball mill maintenance costs?
Absolutely. Stabilizers mitigate electrical root causes of failures: – Reduce motor rewinds by smoothing voltage spikes
– Extend bearing/gearbox life by preventing torque fluctuations
– Cut unscheduled downtime by 40–60% in unstable grid regions.
How often should cement ball mill liners be replaced?
Replacement cycles vary based on: – Material hardness (e.g., granite vs. limestone clinker)
– Mill throughput (high-volume mills wear faster)
– Operational hours
Generally, diaphragm plates last 6–12 months, while shell liners endure 12–24 months. Monitor thickness quarterly.
Why pair voltage stabilizers with VFDs for ball mills?
Voltage stabilizers condition incoming power, while VFDs control motor speed. Together, they: – Enable soft-starting to cut mechanical stress
– Maintain speed accuracy despite grid fluctuations
– Reduce harmonic distortion that destabilizes mills.
This duo can slash energy use by 15–25%.