In the fast-paced world of construction and bulk material handling, cement loading chutes play a critical role in maintaining operational efficiency and environmental compliance. These specialized transfer systems enable rapid, dust-free loading of cement powder from silos to tanker trucks, railcars, or ships. As global infrastructure demands increase and environmental regulations tighten, the innovation in cement chute technology has accelerated, transforming them from simple gravity tubes into sophisticated engineering solutions that maximize productivity while minimizing ecological impact.
How Cement Loading Chutes Work
Cement loading chutes operate on precision-engineered principles to handle fine particulate materials that pose unique handling challenges:
- Gravity-Fed Conveyance:
Cement flows from silos through telescoping sections that extend downward to the transport vessel - Dust Containment System:
Multiple-stage filters and pressure vacuums capture airborne particles - Programmable Flow Control:
Automated systems regulate feed rate based on vessel position and capacity - Sealing Mechanisms:
Flexible skirts or inflatable collars create airtight connections
This orchestrated process reduces loading times from hours to minutes while preventing the escape of fine cement particles—a major environmental and health concern in material handling operations.
Types of Cement Loading Chutes
1. Telescopic Spout Chutes
Most common design featuring nested concentric tubes
– Advantages: Height adaptability, simple maintenance, low power requirements
– Best For: Loading facilities with variable vehicle height
2. Flexible Accordion Chutes
Fabric-reinforced rubber bellows with steel rings
– Advantages: Extreme height versatility, shock absorption, compact storage
– Best For: Multi-product facilities handling varied materials
3. Rigid Spout Systems
Fixed angular chutes with adjustable discharge hoods
– Advantages: Maximum abrasion resistance, zero electricity requirement
– Best For: High-capacity operations with consistent vessel heights
4. Retractable Ship Loaders
Full-length cantilevered systems for marine terminals
– Advantages: Remote vessel positioning, integrated weighing systems
– Best For: Marine terminal operations with high daily throughput
Critical Design Components
Modern cement chutes integrate specialized components to optimize performance:
Component | Function | Innovation Highlights |
---|---|---|
Vortex Flow Regulators | Controls powder velocity | Aerodynamic vanes eliminating particle separation |
Multi-Stage Filtration | Captures airborne dust | Self-cleaning cartridge filters with 99.97% efficiency |
Smart Positioning | Maintains ideal chute-to-vessel distance | Lidar sensors with autotracking algorithms |
Composite Liners | Reduces material buildup | Ultra-smooth PTFE coatings with <5° contact angle |
Condition Monitoring | Predictive maintenance | Vibration, temperature and wear sensors with IoT connectivity |
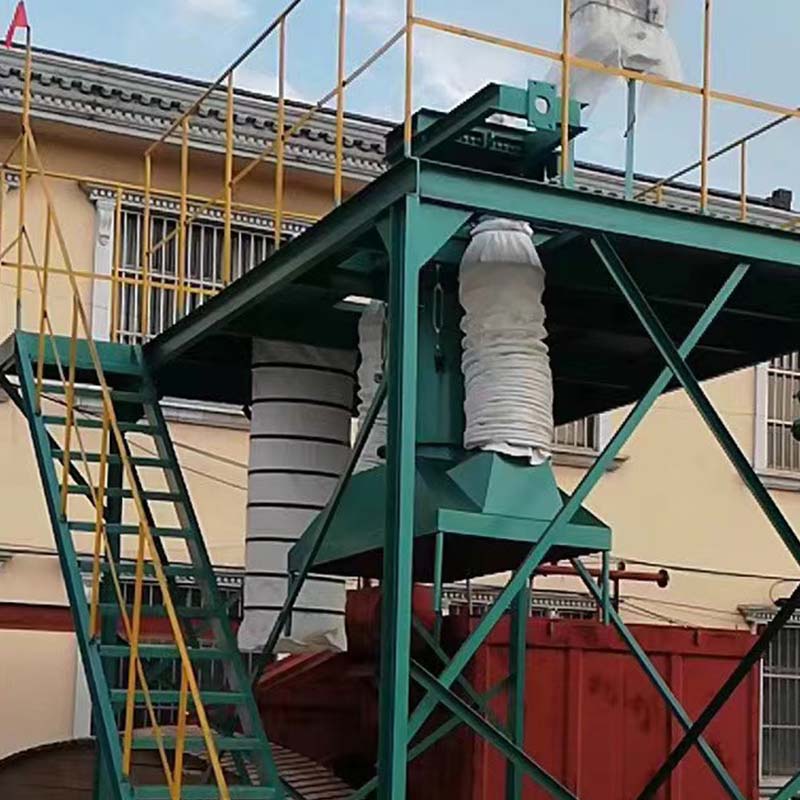
5 Key Benefits of Modern Cement Chutes
Environmental Compliance
Advanced dust collection systems capture >99.5% of airborne particles, keeping facilities below 10mg/m³ emission limits required by EPA and EU regulations. Case studies show dust reduction from 250g/ton to <5g/ton of cement transferred.Operational Efficiency
Automated systems load standard tankers in 7-12 minutes—60% faster than manual methods. Real-time load monitoring and automated shutoff prevent overfills, eliminating costly product losses exceeding $250,000 annually at medium-sized plants.Material Conservation
Precision flow control and sealed transfers reduce product loss to <0.05% compared to 1-3% in open loading systems. For a facility handling 500,000 tons annually, this represents savings of 4,750+ tons of cement.Enhanced Safety
Remote operation eliminates worker exposure to moving equipment and airborne particulates. Integrated explosion venting and static dissipation systems mitigate combustion risks associated with cement dust clouds.Adaptive Intelligence
AI-powered systems continuously optimize loading parameters:- Dynamic Material Sensing: Adjusts flow based on real-time powder characteristics
- Predictive Maintenance: Foresees component wear 200+ operating hours in advance
- Self-Diagnostics: Performs 87-point system checks before each loading cycle
Addressing Industry Challenges
Problem: Product Degradation
Fine cement particles are vulnerable to moisture absorption during transfer.
Solution:
– Nitrogen inerting systems maintain oxygen levels below 8%
– Chutes with thermal jackets prevent condensation
– Hermetic quick-release couplers
Problem: Cross-Contamination
Residual product remaining after material changes.
Solution:
– “Clean-in-Place” rotary air blasters
– Smooth-bore construction with zero trapping points
– Material-shedding nano-coatings
Problem: Vessel Positioning
Tankers frequently misalign by 6-12 inches during loading.
Solution:
– Automated spout repositioning guided by laser alignment
– Machine vision systems verifying hatch locations
Maintenance & Safety Protocols
Essential Maintenance Schedule
Frequency | Tasks |
---|---|
Daily | Filter differential pressure checks, seal integrity inspection, control calibration |
Weekly | Internal wear inspection, motion component lubrication, emergency stop verification |
Monthly | Filter element cleaning/replacement, electrical continuity testing, explosion protection systems inspection |
Annually | Full structural inspection, bearing replacement, liner thickness measurement |
Critical Safety Features
- Dual Emergency Stops: Redundant pull-cord systems
- Grounding Verification: Static dissipation below 10 megohms
- Intrinsic Safety Barriers: Prevent spark generation in hazardous zones
- Guardian System: Blocks chute retraction when sensors detect personnel in danger zone
Future Advancements in Loading Technology
Cement handling technology is evolving toward autonomous systems:
Predictive Flow Modeling:
Machine learning algorithms pre-adjust flow characteristics based on cement chemistry and weather dataCarbon Tracking Systems:
Integrated sensors quantifying emissions throughout the loading cycle for ESG reportingHydrogen-Powered Loaders:
Converting diesel-powered mobile units to emission-free operationsBlockchain Integration:
Immutable loading records ensuring quality assurance across logistics chains