The belt conveyor roller is an essential component of any belt conveyor system. Rollers come in all kinds and make up about 35% of what a conveyor system costs, plus they create more than 70% of the resistance. Therefore, the quality of these rollers is extremely important. They are available in both steel and plastic materials.
Purpose of Belt Conveyor Rollers
The primary function of the roller is to support the weight of the conveyor belt and the materials being transported. Rollers must operate flexibly and reliably. Reducing friction between the conveyor belt and the rollers is key to extending the lifespan of the belt, which represents over 25% of the total conveyor cost. Although rollers may seem like a small component with a simple structure, manufacturing high-quality rollers is a challenging task.
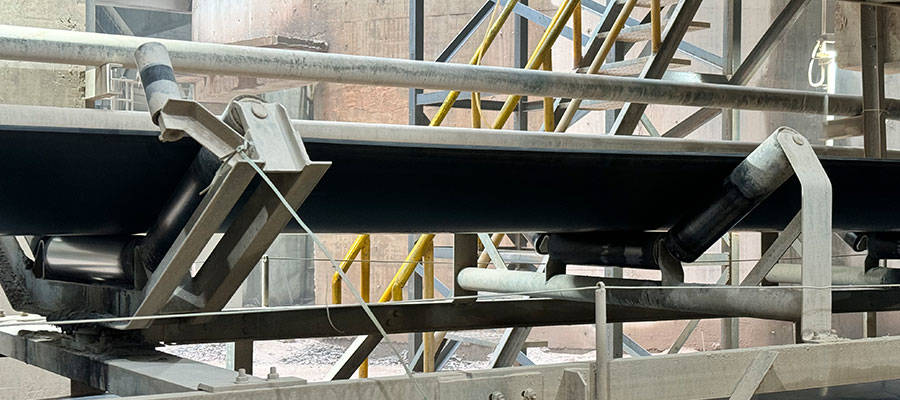
Quality Standards for Belt Conveyor Rollers
To determine the quality of a roller, consider the following criteria:
- Radial Runout: The amount of deviation in the roller’s rotation.
- Roller Flexibility: The ease with which the roller spins.
- Axial Movement: The degree of lateral movement along the roller’s axis.
Types of Belt Conveyor Rollers
- Material Types:
- Rubber Rollers
- Ceramic Rollers
- Nylon Rollers
- Insulated Rollers
- Main Categories:
- Trough Rollers: Includes standard, forward-tilt, quick-change bearing, suspension, triple-chain, reversible, variable trough angle, transition, and V-type rollers.
- Parallel Rollers: Includes standard, comb-type, forward-tilt, steel-rubber composite, and spiral rollers.
- Self-aligning Rollers: Features general-purpose, friction-reversible, heavy-duty, cone-shaped, spiral, and combination rollers.
- Buffer Rollers: Includes spring plate, buffer ring, heavy-duty buffer, adjustable elasticity, and suspension rollers.
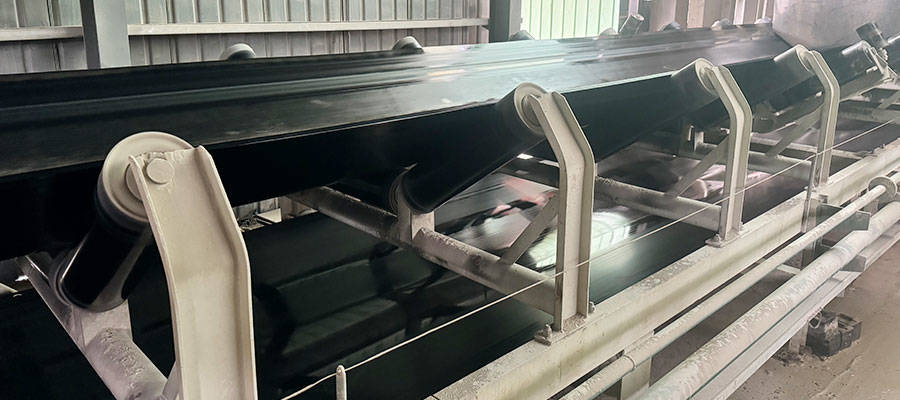
Working Principle
Belt conveyor rollers operate through the friction between the conveyor belt and the roller. This friction drives the roller body, bearing housing, outer bearing, and sealing ring to rotate. They work hand in hand with the conveyor belt to make moving materials a breeze.
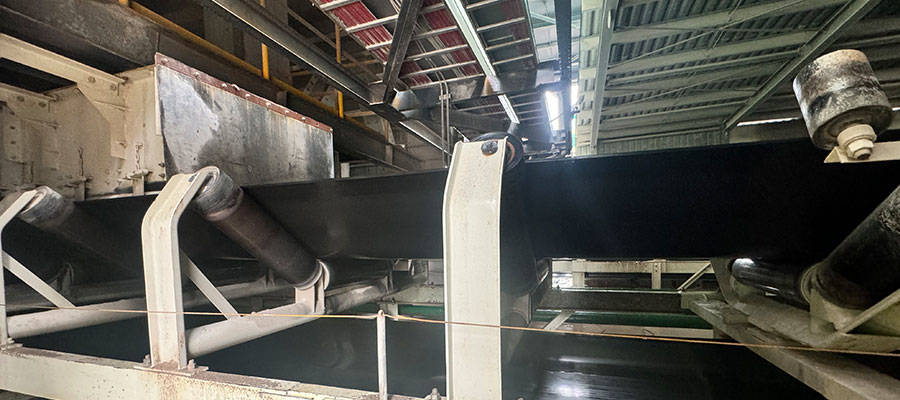
Three Roll Trough
This standard idler design is commonly used in most heavy-duty conveyor applications. Darko manufacturer make the rollers from steel and often coat them with multiple layers of specific paint, rubber, or other anti-corrosive materials.
The rollers may be in steel, covered with several layers of a particular specifi cation of paint, or covered in rubber or in other anti corrosive materials.
Roller Series and Applications
These rollers are particularly suited for conveyors operating in challenging conditions, where working loads are high and large lump sizes are conveyed. Despite these demands, they require minimal maintenance. Typical applications include mines, cement works, coal-fired power plants, and dock installations.
The roller sealing system effectively addresses environmental challenges such as dust, dirt, water, and extreme temperatures. Standard greased components function well within a temperature range of -20°C to +100°C. For applications outside this range, special grease, bearings, and seals can be used.
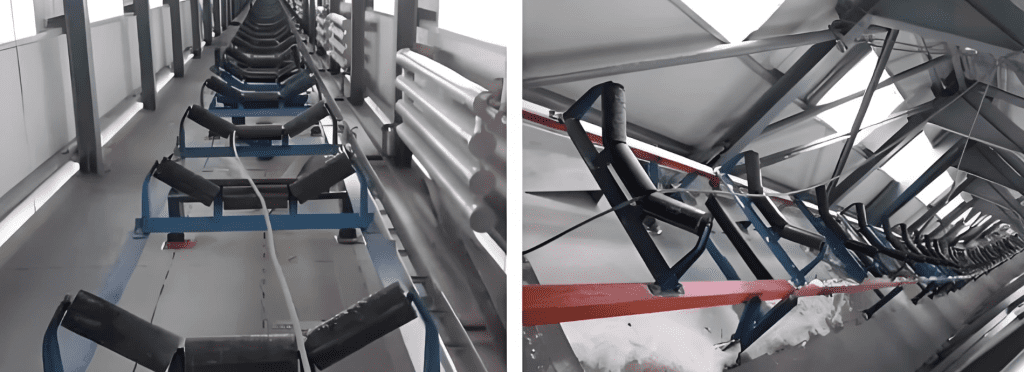
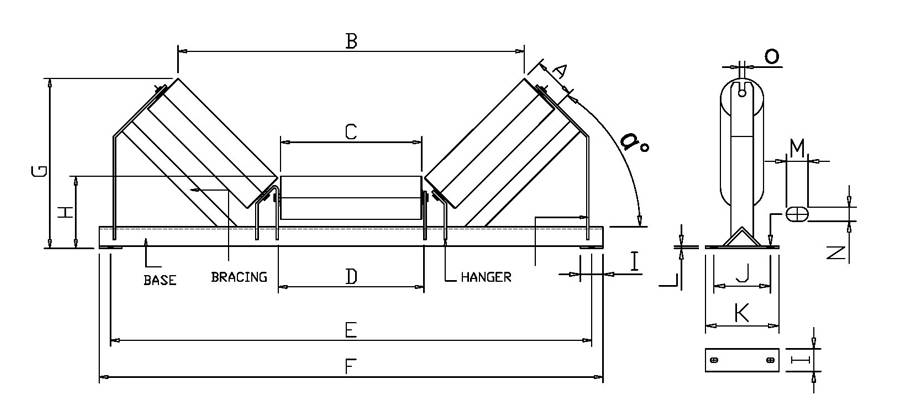
You May Also Like
![]() | ![]() | ![]() |
![]() | ![]() | ![]() |
Darko is among the fabric filters manufacturers in China. We have been supplying small and large companies with safe and ISO-certifed fabric filters wholesale. We provide industrial fabric filters of various specifications an custom sizes.
Darko has been working as a trust worthy fabric filter manufacturer and supplier in China for more than 10 years. With our years of experience in the industry, we can guarantee the production of high-quality Chinese fabric filters. Aside from manufacturing facilities in our own factory we also offer customization and design services to our customers. We produce fabric filters to process various air volume .
If you are looking for a filter company, you can rely on Darko. Buy fabric filters in bulk from us and let us help you grow your business using our customizable and affordable products.