In the fast-paced world of industrial automation, transportadores de corrente stand as one of the most reliable and versatile solutions for moving materials efficiently. Whether in manufacturing plants, warehouses, or packaging facilities, these robust systems form the mechanical arteries that keep production lines flowing. A chain conveyor is a type of mechanical handling equipment designed to transport materials, products, or components using an endless chain loop driven by sprockets. Unlike belt conveyors that use flexible belts, chain conveyors employ metal chains (often with attachments) to provide superior strength, durability, and adaptability for heavy or irregular loads. This article explores the workings, types, applications, and innovations of chain conveyors — essential components in modern material handling.
A Brief History of Chain Conveyors
The concept of chain-driven conveyance dates back centuries, with early examples in water-powered mills and agricultural machinery. However, the Industrial Revolution catalyzed their evolution. In the late 19th century, chain conveyors gained prominence in coal mines and automotive assembly lines. Henry Ford’s moving assembly line (1913) famously used chain-driven conveyors to revolutionize manufacturing, slashing Model T production time from 12 hours to 93 minutes. Post-WWII, advancements in metallurgy and engineering enabled chains to handle heavier loads at higher speeds, cementing their role in diverse industries from food processing to automotive manufacturing.
How Chain Conveyors Work
Chain conveyors operate on a simple yet effective principle:
- Power Transmission: An electric motor drives a drive sprocket, which engages with the chain links.
- Chain Movement: The chain loops around drive and tail sprockets, forming an endless track.
- Load Support: Materials ride directly on the chain or on attached flights, slats, or platforms.
- Guidance & Tension: Idlers, guides, and tensioners maintain alignment and optimal chain tension.
- Sistema de controlo: Sensors, VFDs (Variable Frequency Drives), and PLCs regulate speed, direction, and stops.
Key distinctions from belt conveyors include: – Positive Drive: Chains mesh with sprockets, preventing slippage under load. – Heavy-Duty Design: Metal chains tolerate high temperatures, abrasion, and impact. – Attachment Versatility: Fixtures like pushers, cleats, or magnets can be added to handle specific loads.
Core Components of a Chain Conveyor System
Understanding a chain conveyor requires familiarity with its anatomy:
- Chains:
- Roller Chains: Feature cylindrical rollers for smooth engagement with sprockets. Common in general material handling.
- Leaf Chains: Comprise stacked plates for high tensile strength (ideal for lifts and hoists).
Forged Chains: Robust and corrosion-resistant for extreme conditions (e.g., mining).
Sprockets:
- Drive Sprocket: Connected to the motor, transferring torque to the chain.
Idler/Tail Sprocket: Guides the return path of the chain and maintains tension.
Anexos:
Flights (paddles for bulk solids), slats (platforms for unit loads), or custom fixtures (hooks, trays).
Frame & Supports:
Structural rails or channels that align and support the chain and product loads.
Unidade de acionamento:
Electric motor, gearbox, and couplings providing controlled power.
Dispositivo de tensionamento:
Screw or pneumatic mechanisms to adjust chain slack.
Controls:
- Sensors, timers, and automation interfaces for seamless integration into production lines.
Types of Chain Conveyors and Their Applications
Chain conveyors are broadly categorized by design and function:
- Drag Chain Conveyors:
- Design: Chains move materials in troughs via flights or crossbars.
- Utilizações: Ideal for heavy bulk materials like grains, cement, or wood chips.
Indústrias: Agriculture, mining, waste management.
Slat Chain Conveyors:
- Design: Chains with attached slats form a continuous moving platform.
- Utilizações: Perfect for heavy or irregularly shaped items (e.g., pallets, drums, car engines).
Indústrias: Automotive assembly, bottling plants, heavy machinery.
En-Masse Conveyors:
- Design: Material moves en masse with the chain in a sealed casing.
- Utilizações: Gentle handling of fragile bulk solids (powders, granules) with minimal degradation.
Indústrias: Food processing, chemicals, plastics.
Apron Chain Conveyors:
- Design: Overlapping metal plates on chains create a “pan” surface.
- Utilizações: High-temperature or abrasive materials (ore, slag, hot castings).
Indústrias: Steel mills, foundries, mining.
Overhead Chain Conveyors:
- Design: Chains run on I-beams or tracks above workstations.
- Utilizações: Suspended transport (e.g., painting lines, garment production).
- Indústrias: Automotive, aerospace, textiles.
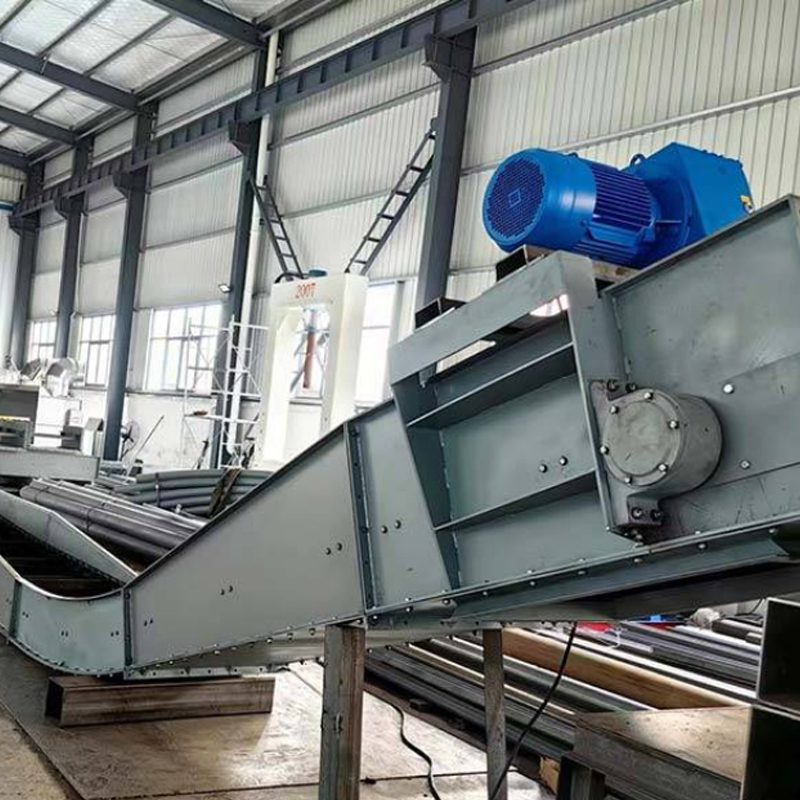
Advantages of Chain Conveyors
- High Load Capacity: Handle weights from kilograms to tons with minimal deflection.
- Durabilidade: Metal chains withstand harsh environments (heat, chemicals, abrasion).
- Manutenção reduzida: Fewer breakdowns compared to belts; simple chain/sprocket replacement.
- Versatilidade: Customizable lengths, speeds, and attachments for specialized tasks.
- Precision: Ideal for synchronous assembly lines due to positive drive.
- Low Slip: Minimal slippage ensures reliable positioning for automation.
Limitations and Challenges
- Noise: Metal-on-metal contact generates higher noise than belt systems (requires acoustic enclosures).
- Peso: Heavier construction increases installation complexity and cost.
- Lubrication Needs: Regular lubrication essential to reduce wear and prevent corrosion.
- Consumo de energia: Higher power requirements compared to belt conveyors for similar loads.
- Limited Flexibility: Generally unsuitable for tight curves or steep inclines without specialized designs.
Applications Across Industries
Chain conveyors are ubiquitous in sectors demanding reliability and strength:
- Automotive: Engine block transfers, chassis assembly, painting lines.
- Food & Beverage: Pallet handling, oven/conveyor baking, bottle/can sorting.
- Packaging: Case palletizing, tray sealing, filling machines.
- Warehousing/Logistics: Pallet conveyors for AS/RS (Automated Storage/Retrieval Systems).
- Mining/Quarrying: Transporting ore, gravel, and slag in rugged environments.
- Recycling: Moving scrap metal, plastic fragments, or municipal waste.
.
Selecting the Right Chain Conveyor
When designing or retrofitting a system, consider:
- Load Characteristics: Weight, size, shape, and fragility.
- Environment: Temperature, humidity, and exposure to corrosive agents.
- Throughput: Required speed (m/s) and volume (tons/hour).
- Layout: Distance, inclines/declines, curves, and integration with other equipment.
- Maintenance Access: Ease of inspection, lubrication, and chain replacement.
- Regulations: Industry-specific standards (e.g., FDA for food, ATEX for explosives).
Maintenance and Safety Best Practices
- Lubrificação: Use auto-lubricators to reduce wear and friction.
- Inspection: Regularly check chains for elongation, sprocket alignment, and cracked links.
- Tensioning: Maintain optimal tension to prevent derailment or slippage.
- Safety Features: Install emergency stops, guards, and anti-jam sensors.
- Operator Training: Ensure staff understands lockout/tagout (LOTO) procedures and hazard zones.
- Limpeza: Prevent material buildup to reduce fire risks or contamination (critical in food/pharma).
Innovations and Future Trends
Chain conveyors continue evolving with technology:
- Self-Lubricating Chains: Polymer-embedded bearings minimizing manual lubrication.
- IoT Integration: Smart sensors monitoring chain wear, temperature, and predictive maintenance needs.
- Lightweight Alloys: Aluminum or composite chains reducing energy consumption.
- Hybrid Systems: Combining chains with modular belts for enhanced flexibility.
- Hygienic Designs: Wash-down compatible materials for sanitary industries.
- Sustainable Engineering: Recyclable chains and energy-efficient motors lowering carbon footprints.
Chain conveyors remain indispensable in industrial material handling due to their unmatched strength, reliability, and adaptability. From dragging tons of ore in mines to assembling delicate electronics, they bridge the gap between manual labor and full automation. As industries pursue higher efficiency and sustainability, innovations in chain technology will continue to refine these workhorses of conveyance. Whether upgrading an existing line or designing a new facility, selecting the right chain conveyor is a strategic investment in operational resilience — proving that even in the age of robotics, the humble chain still links success in modern manufacturing.