As emissões de poeiras na produção de aço são responsáveis por mais de 15% da poluição industrial por partículas. Com regulamentos ambientais mais rigorosos, os colectores de sacos tradicionais não cumprem frequentemente as normas de eficiência. Os colectores de poeiras de cartucho oferecem uma alternativa compacta e de elevado desempenho - mas o seu sucesso depende de uma aplicação correta. Este guia explora como as siderúrgicas podem aproveitar a tecnologia de cartucho, evitando armadilhas comuns.
1. Princípio de funcionamento e caraterísticas dos colectores de pó de cartucho
1.1 Como funcionam os colectores de pó de cartucho
Colectores de pó de cartucho utilizam cartuchos como elemento filtrante e empregam a tecnologia de jato pulsante para a remoção de poeiras. O princípio de funcionamento envolve a aspiração de ar empoeirado para o interior da caixa através do exaustor, das condutas e da entrada de ar. À medida que o fluxo de ar se expande subitamente e interage com a placa de distribuição de ar, as partículas de pó maiores caem diretamente no depósito de pó devido à gravidade e à inércia. As partículas mais pequenas e mais leves passam através do cartucho, onde são capturadas pelo material filtrante através da difusão Browniana e dos efeitos de peneiração. Após a retrolavagem, o pó cai no depósito de pó para reciclagem, enquanto o ar limpo é descarregado através do tubo de exaustão com a ajuda de um ventilador.
1.2 Principais vantagens
► Eficiência de filtragem em conformidade com a OSHA:Os cartuchos utilizam fibras de poliéster importadas como meio filtrante. Apresentam uma camada de fibras sub-micrónicas ultra-finas que bloqueiam eficazmente a maioria das partículas de poeira sub-micrónicas, alcançando uma eficiência de filtragem de até 99,99%, cumprindo as normas de emissões ultra-baixas.
► Conceção de baixa resistência: Graças à grande área de filtragem e à baixa velocidade de filtragem, a resistência de funcionamento não excede tipicamente os 1000 Pa. Isto reduz a carga operacional e os custos do sistema de recolha de poeiras.
►Estrutura compacta: A conceção dos cartuchos ocupa um espaço mínimo, facilitando a instalação e a substituição. Os cartuchos são geralmente mais curtos do que os filtros de mangas, simplificando a construção e a manutenção.
►Longa vida útil: Os cartuchos utilizam fibras de poliéster importadas, obtendo uma filtragem submicrónica de 99,99% - cumprindo as rigorosas normas de emissão das fábricas de aço.
►Reutilizável: Os cartuchos de poliéster e os cartuchos cobertos por membrana podem normalmente ser lavados com água e reutilizados, reduzindo os custos de aquisição.
1.3 Limitações a considerar
⚠️ Não para aplicações com elevado teor de humidade Em ambientes húmidos, os cartuchos podem ficar bloqueados, exigindo tempo de paragem para substituições, o que afecta a eficiência da produção.
⚠️ Custo mais elevado vs Filtros Baghouse: O preço unitário do cartucho do filtro é 5 a 8 vezes superior ao de um saco de pano normal, mas a vida útil global é melhor.
2. Caraterísticas das poeiras da produção de aço
Dados críticos para a seleção do coletor de pó:
Área de produção | Distribuição do tamanho das partículas | Teor de humidade | Gama de temperaturas |
---|---|---|---|
Material de sinterização | N/A | >6% | 50-80°C |
Alto-forno | 76-84% abaixo de 200 malhas | <1% | 100-150°C |
Aciaria BOF | >5μm (98%) | 1.0-1.5% | 80-120°C |
2.1 Área de matérias-primas de sinterização
Devido a problemas de transporte, os minérios nacionais e estrangeiros têm geralmente um teor de humidade superior a 6%. A utilização de armazéns fechados e a supressão de poeiras por pulverização agravam ainda mais as emissões de poeiras.
2.2 Produto sinterizado e área de depósito de minério
1. os produtos sinterizados geram partículas de pó que variam entre 0,8 e 61,0 μm durante o transporte, com um teor de humidade inferior a 1%.
2. os altos-fornos utilizam normalmente técnicas de moagem aquecida, com partículas abaixo de 200 mesh, compreendendo 76% a 84%, e teor de humidade também abaixo de 1%.
3. durante o transporte de coque, o teor de humidade é inferior a 1% para os processos de têmpera a seco, enquanto os processos de têmpera húmida excedem frequentemente 10%.
2.3 Área de produção de aço conversor
1. os fluxos utilizados nos conversores têm normalmente um teor de humidade de 1,0% a 1,5%.
2.As poeiras geradas durante o processo de fabrico de aço têm mais de 98% de partículas maiores que 5 μm, com baixas temperaturas.
3. o teor de humidade das poeiras resultantes do manuseamento das escórias do conversor é frequentemente superior a 10%.
2.4 Área de produção de aço para laminagem
As emissões de gases húmidos durante os processos de laminagem excedem normalmente a humidade de 10%, principalmente devido ao arrefecimento com água.
2.5 Área de produção de coque
1. as poeiras de carvão geradas durante a área de preparação do coque têm frequentemente um teor de humidade superior a 6%, com mais de 99% de partículas de dimensão superior a 2 μm.
2. o tamanho das partículas de poeira durante o empurrão de carvão geralmente varia de 3,3 a 4,7 μm, com umidade de gás residual entre 1% e 5%.
2.6 Área de produção do Flux
Durante o transporte de calcário e cal acabada, mais de 95% de partículas de poeira excedem 10 μm, com teor de humidade inferior a 1%.
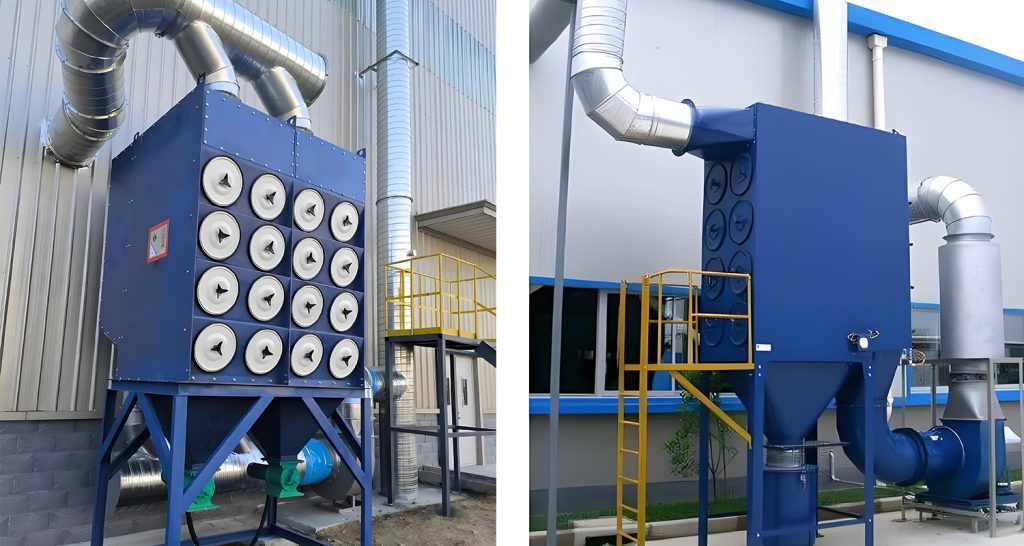
3. Recomendações fundamentais para aplicações de colectores de pó de cartucho em instalações siderúrgicas
① Estratégias de controlo da humidade
Evite recolher gases residuais com elevada humidade: Isto inclui os gases residuais do minério de ferro na fase de preparação da sinterização e dos processos de coqueificação húmida.
Para controlo de poeiras em conformidade com a OSHAMonitorize os níveis de humidade nos pontos de transferência de materiais.
② Manuseamento de partículas pegajosas
Tenha cuidado com gases residuais pegajosos: Isto aplica-se às poeiras geradas durante o transporte da cal e no processo de coqueificação.
Nota: As poeiras pegajosas com um teor de humidade >5% podem exigir um pré-tratamento.
③ Otimização do fluxo de ar
Optimize o design da entrada: Reduza a velocidade do ar de entrada do coletor de pó de cartucho e melhore a distribuição interna do fluxo de ar para garantir um fluxo uniforme entre os cartuchos.
Recomendado velocidade de entrada: ≤1,2 m/s para a maioria das aplicações em aço.
④ Manutenção do sistema de jato de impulsos
Assegure um fluxo de ar uniforme na lavagem por retorno: O comprimento do bocal de retrolavagem deve ser maximizado para manter uma distribuição uniforme do fluxo de ar.
Melhores práticas: Inspeccione o alinhamento dos bicos trimestralmente.
⑤ Protocolos de garantia de qualidade
Controlo rigoroso da qualidade dos cartuchos: Certifique-se de que os parâmetros técnicos dos cartuchos dobrados cumprem as normas relevantes. Inspeccione a qualidade da membrana e a uniformidade das dobras e verifique o processo de fabrico dos selos dos cartuchos.
Certificação: Procure filtros em conformidade com a norma ISO 16890.
Em conclusão, os colectores de pó de cartucho são muito promissores para utilização em empresas siderúrgicas. No entanto, a otimização do design e das estratégias de utilização com base em condições de funcionamento específicas é essencial para melhorar a eficiência da remoção de poeiras e a relação custo-eficácia. Escolha os colectores de pó de cartucho da Darko para um desempenho excecional e soluções fiáveis.
Para mais informações sobre os nossos produtos ou para obter aconselhamento profissional, não hesite em contactar contactar-nos!