Como equipamento central das fábricas e linhas de produção modernas, transportadores de correia desempenham um papel insubstituível na melhoria da eficiência e na redução dos custos de mão de obra. No entanto, falhas comuns, como desvios de correia, fugas de material e incêndios, não só afectam a eficiência da produção, como também podem causar graves acidentes de segurança. Este artigo analisará em pormenor as causas destas falhas e fornecerá medidas preventivas práticas e viáveis.
Análise de falhas comuns
1. Problema de desvio da correia
Sendo o fenómeno de falha mais típico, a sua solução deve ser orientada:
- Ajuste do grupo de rolos de rolamento: Para o desvio no meio, a posição pode ser ajustada utilizando o orifício em forma de cintura do suporte de rolos
- Aplicação do conjunto de rolos auto-ajustáveis: A correção automática é conseguida através da geração de impulso lateral, adequado para transportadores de curta distância ou bidireccionais, mas deve ter cuidado ao utilizar transportadores de longa distância para evitar afetar a sua vida útil
- Calibração dos rolos de transmissão: Certifique-se de que todos os rolos estão perpendiculares à linha central do transportador. Em caso de desvio, ajuste a posição do assento da chumaceira de acordo com o princípio de "marcha apertada, não marcha solta"
- Inspeção do dispositivo de tensionamento: Certifique-se de que o eixo do tambor tensor é perpendicular à correia e de que a tensão em espiral/hidráulica tem de garantir que os assentos dos rolamentos de ambos os lados se movem em sincronia
- Otimização do ponto de queda do material: O impacto do material é um fator importante e é necessário ajustar a altura e o ângulo relativos dos transportadores superior e inferior
- Ajuste do funcionamento bidirecional: Duas direcções de funcionamento têm de ser depuradas separadamente, com destaque para o ajuste da transmissão e do tambor de inversão
2. Fenómeno de fuga de material
Isto ocorre principalmente nas seguintes fases:
- Ponto de reprodução: Os danos ou a sobrecarga da placa da saia de borracha na ranhura da guia são a causa principal, sendo necessário reforçar a inspeção e a manutenção
- Material suspenso na secção côncava: Devido ao pequeno raio de curvatura da secção de transição, o raio da secção côncava deve ser aumentado durante o projeto
- O desvio provoca a dispersão: a correção atempada pode resolver eficazmente o problema da dispersão dos bordos
3. Rastreabilidade dos acidentes de segurança
Causas dos acidentes de incêndio
Caracteriza-se pela rapidez e disseminação rápida:
- Aquecimento escorregadio: A tensão insuficiente, a sobrecarga ou a diminuição do coeficiente de atrito podem provocar incêndios a altas temperaturas
- Avarias eléctricas: curto-circuitos, explosões de equipamentos e outros problemas eléctricos
Causas dos acidentes de desvio
O desalinhamento da correia pode reduzir o tempo de vida útil do transportador e conduzir a períodos de inatividade e a problemas de segurança. As principais causas são:
- Falha mecânica: falha do cilindro hidráulico, encravamento do rolo, etc.
- Defeito de instalação: desvio do posicionamento inicial
- Deficiência de manutenção: Material acumulado não eliminado atempadamente
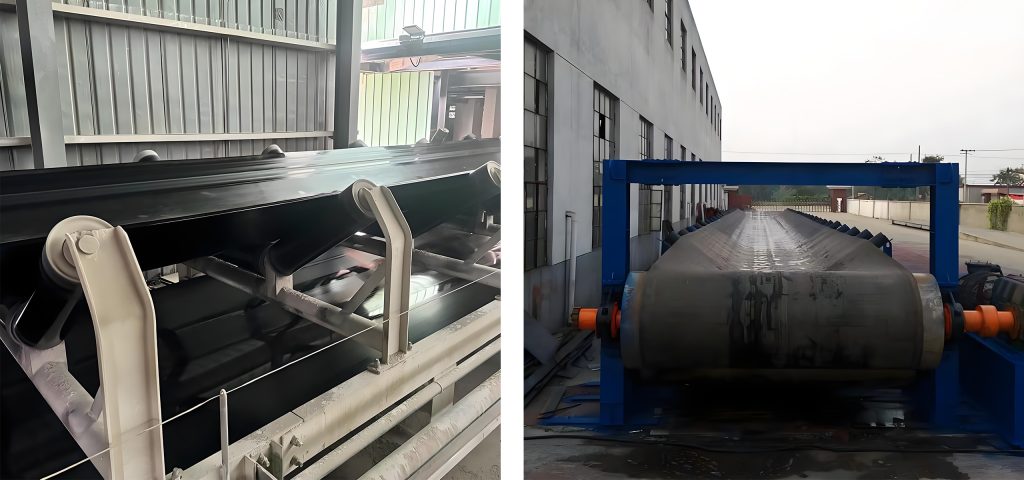
Plano de prevenção sistemático
1、 Accionadores de alta temperatura
Operação de sobreaquecimento do fumo
- Condições de funcionamento típicas: fornos metalúrgicos (>300 ℃), fornos rotativos de cimento (250-350 ℃)
- Limite de material:
Material filtrante de poliéster: pode suportar 130-150 ℃ continuamente
○ Material filtrante Nomex: até 204 ℃
Material do filtro de fibra de vidro: 260 ℃ (tratado com óleo de silicone)
- Mecanismo de falha: A temperatura elevada provoca a rutura das cadeias moleculares das fibras e, após uma diminuição da resistência, estas são facilmente inflamadas por faíscas
Fenómeno de sobreaquecimento local
- Desencadeadores comuns:
Distribuição irregular do fluxo de ar (diferença de velocidade do vento medida >30%)
Avaria do sistema de limpeza de poeiras (a taxa de falha da válvula de impulso atinge 15%)
○ Má permuta de calor (a diferença de temperatura excede o valor de projeto em 50℃)
2. acumulação de material combustível
Caraterísticas da combustão espontânea de poeiras
Tipo de pó | Ponto de ignição (°C) | Energia mínima de ignição (mJ) |
---|---|---|
Pó de carvão | 160-180 | 30 |
Pó de alumínio | 550 | 15 |
Enxofre | 190 | 1.5 |
2. Consequências da falha do sistema de limpeza
A taxa de libertação de calor de oxidação aumenta em 300% quando a espessura da camada de poeira excede 3mm.
Estudo de caso: Numa fábrica de cimento, 5 mm de acumulação de pó nos sacos de filtro devido a falha da válvula solenoide acionado combustão espontânea.
Perigos de descarga eletrostática
1. Mecanismo de produção de eletricidade
- O processo de transporte de poeiras pode gerar uma tensão estática de 10-30kV
- Os sacos de filtro de fibras químicas são propensos a acumular cargas quando a resistência da superfície é superior a 10 ¹³ Ω
2. Condições de ignição da descarga
Como um fabricante profissional de equipamento de transporte, Dako sempre se empenhou em fornecer equipamentos de alto desempenho que foram submetidos a testes rigorosos.
Ao implementar as medidas preventivas acima, a taxa de falha do equipamento pode ser significativamente reduzida, proporcionando proteção para uma produção segura. Se precisar de mais apoio técnico, não hesite em contactar a nossa equipa de engenharia a qualquer momento.
Dica quente: a manutenção regular é a chave para prolongar a vida útil do equipamento!